Blast-furnace ironmaking energy-saving novel process and equipment
A blast furnace ironmaking and new process technology, applied in the field of smelting, can solve problems such as the adverse effects of ironmaking quality and energy consumption, the reduction of melting speed and dripping speed, and the influence of blast furnace air permeability, etc. The effect of improving performance and simplifying the burden of uneven heating and cooling
- Summary
- Abstract
- Description
- Claims
- Application Information
AI Technical Summary
Problems solved by technology
Method used
Image
Examples
Embodiment Construction
[0029] The technical solutions of the present invention will be described in detail below in conjunction with specific implementation methods and accompanying drawings.
[0030]The new energy-saving blast furnace ironmaking process of the present invention includes mechanical manufacturing steps, pelletizing steps, direct reduction steps, and vacuum cooling steps. The pelletizing step is to use a cantilever briquetting machine to shape the blended iron ore powder It is a mineral powder ball, which can be divided into 42 pieces at the same time. The appearance diameter of this mineral powder ball is 1000mm, and the height is 200mm (the number and size of the equal parts can be set flexibly according to specific needs, which are related to the specific equipment size and output requirements. The invention is not limited), and then the cantilever is rotated by 90 degrees and then hydraulically pushed to the trolley launched by the circulating direct reduction furnace, and the oper...
PUM
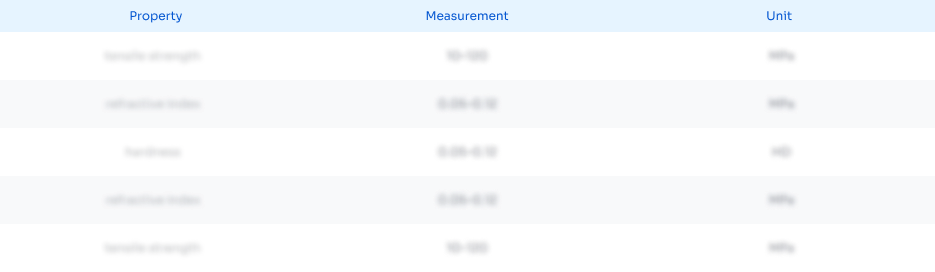
Abstract
Description
Claims
Application Information

- Generate Ideas
- Intellectual Property
- Life Sciences
- Materials
- Tech Scout
- Unparalleled Data Quality
- Higher Quality Content
- 60% Fewer Hallucinations
Browse by: Latest US Patents, China's latest patents, Technical Efficacy Thesaurus, Application Domain, Technology Topic, Popular Technical Reports.
© 2025 PatSnap. All rights reserved.Legal|Privacy policy|Modern Slavery Act Transparency Statement|Sitemap|About US| Contact US: help@patsnap.com