Method for preparing zinc cyanide coproduced with calcium sulfate by utilizing cyanide melt slag
A technology of calcium sulfate and zinc cyanide, applied in the directions of metal cyanide, calcium/strontium/barium sulfate, etc., can solve the problems of difficult control, complicated operation, unfavorable popularization and application, etc., and achieves less equipment investment and operation steps. Simple and suitable for promotion and application
- Summary
- Abstract
- Description
- Claims
- Application Information
AI Technical Summary
Problems solved by technology
Method used
Image
Examples
Embodiment 1
[0034] A method for preparing zinc cyanide co-production calcium sulfate with cyanide melt waste slag, comprising the following specific steps:
[0035] A: Take 500kg of cyanide melt waste residue containing calcium cyanide, calcium sulfate and hydrogen cyanide, wherein the content of hydrogen cyanide is 150g, and the content of hydrogen cyanide is 50kg, and put it into the pipeline for reaction with excess zinc sulfate with a mass concentration of 10%. In the device (1), the chemical reaction is carried out at a temperature lower than 40°C;
[0036] B: when the reaction was carried out for 2 hours, the reaction product was suction-filtered in a suction filter pump (2), to obtain clarified cyanide filtrate and calcium sulfate filter cake;
[0037] C: the clarified cyanide filtrate is sent to the vacuum distiller (3), carries out vacuum distillation at 45 DEG C, and then cools to obtain a mixed solution containing zinc cyanide crystals;
[0038] D: Filter the mixed solution co...
Embodiment 2
[0041] A method for preparing zinc cyanide co-production calcium sulfate with cyanide melt waste slag, comprising the following specific steps:
[0042] A: Take 500kg of cyanide melt waste residue containing calcium cyanide, calcium sulfate and hydrogen cyanide, wherein the content of hydrogen cyanide is 200g, the content of hydrogen cyanide is 50kg, and the excess zinc sulfate with a mass concentration of 8% is put into the pipeline In the reactor (1), the chemical reaction is carried out at a temperature lower than 45°C;
[0043] B: when the reaction was carried out for 4 hours, the reaction product was suction-filtered in the suction filter pump (2), to obtain clarified cyanide filtrate and calcium sulfate filter cake;
[0044] C: the clarified cyanide filtrate is sent to the vacuum distiller (3), carries out vacuum distillation at 40 DEG C, and then cools to obtain a mixed solution containing zinc cyanide crystals;
[0045] D: Filter the mixed solution containing zinc cya...
Embodiment 3
[0048] A method for preparing zinc cyanide co-production calcium sulfate with cyanide melt waste slag, comprising the following specific steps:
[0049] A: Take 500kg of cyanide melt waste residue containing calcium cyanide, calcium sulfate and hydrogen cyanide, wherein the content of hydrogen cyanide is 250g, the content of hydrogen cyanide is 50kg, and the excess zinc sulfate with a mass concentration of 5% is put into the pipeline In the reactor (1), the chemical reaction is carried out at a temperature lower than 50°C;
[0050] B: when the reaction was carried out for 5 hours, the reaction product was suction-filtered in the suction filter pump (2), to obtain clarified cyanide filtrate and calcium sulfate filter cake;
[0051] C: the clarified cyanide filtrate is sent to the vacuum distiller (3), carries out vacuum distillation at 40 DEG C, and then cools to obtain a mixed solution containing zinc cyanide crystals;
[0052] D: Filter the mixed solution containing zinc cyani...
PUM
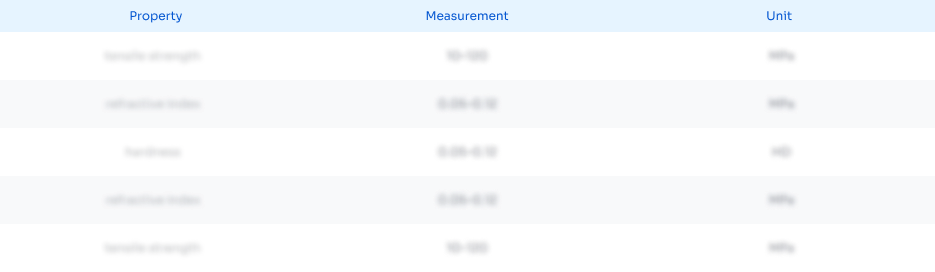
Abstract
Description
Claims
Application Information

- Generate Ideas
- Intellectual Property
- Life Sciences
- Materials
- Tech Scout
- Unparalleled Data Quality
- Higher Quality Content
- 60% Fewer Hallucinations
Browse by: Latest US Patents, China's latest patents, Technical Efficacy Thesaurus, Application Domain, Technology Topic, Popular Technical Reports.
© 2025 PatSnap. All rights reserved.Legal|Privacy policy|Modern Slavery Act Transparency Statement|Sitemap|About US| Contact US: help@patsnap.com