Process for coating automobile axle
A coating process and vehicle axle technology, which is applied to the surface coating liquid device, coating, pretreatment surface, etc., can solve the problems affecting the quality of the vehicle axle, low production efficiency, high cost, etc., to increase product selling points, The effect of improving product quality and reducing production costs
- Summary
- Abstract
- Description
- Claims
- Application Information
AI Technical Summary
Problems solved by technology
Method used
Examples
Embodiment Construction
[0022] The main process of the painting process of the axle of the present invention is: degreasing → hot water washing → anti-rust water washing → water blowing shielding → drying → strong cooling → spraying primer → spraying top paint → leveling → drying → strong cooling. The vehicle axle coating line of the present invention adopts new materials, new technology and advanced 2C1B coating system. cost of running the production line.
[0023] The 2C1B coating system adopted by the axle coating line of the present invention: two coatings and one baking; that is, after the primer is sprayed on the workpiece, it will be leveled and flashed for a short time, and then the topcoat will be wet-on-wet sprayed directly, and the two-layer paint film will be dried. room for one-time drying. After adopting the 2C1B coating system, the primer drying process was canceled, and a corresponding primer drying room was omitted, thereby reducing the investment in fixed assets by about 500,000 yu...
PUM
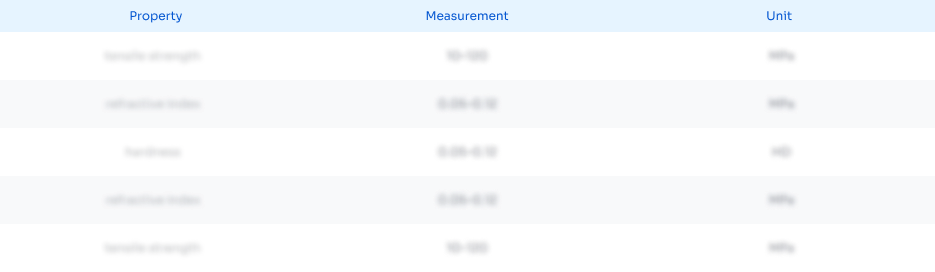
Abstract
Description
Claims
Application Information

- R&D
- Intellectual Property
- Life Sciences
- Materials
- Tech Scout
- Unparalleled Data Quality
- Higher Quality Content
- 60% Fewer Hallucinations
Browse by: Latest US Patents, China's latest patents, Technical Efficacy Thesaurus, Application Domain, Technology Topic, Popular Technical Reports.
© 2025 PatSnap. All rights reserved.Legal|Privacy policy|Modern Slavery Act Transparency Statement|Sitemap|About US| Contact US: help@patsnap.com