Method and device for sensorless bearing damage detection and system identification of an electrical drive system
A technology for electric transmission and detectors, which is applied in the field of electric transmission system, identification of the system and/or detection of damage and devices, and can solve problems such as increasing costs
- Summary
- Abstract
- Description
- Claims
- Application Information
AI Technical Summary
Problems solved by technology
Method used
Image
Examples
Embodiment Construction
[0028] The present invention is distinguished in the following manner, namely, according to figure 1 The small frame 1 in the frame 1 performs the recognition of the mechanical angular velocity in a detector-less manner, that is to say, no separate sensor is used. Instead, only the machine's terminal values are used. Here, for example, according to box 3 the stator current is used to form the torque component and according to box 4 the estimated motor speed is used, which according to box 2 is introduced as signals to be processed by a special signal processing. The specific signal processing of the invention is based on the use of the Welch method or the correlogram method according to box 5, by means of which the frequency response of the mechanism is calculated from the measured time signal (cf. box 6).
[0029] Next to the digital signal processing, according to the small box 7, the transmission system parameters are determined. Depending on the destination, all releva...
PUM
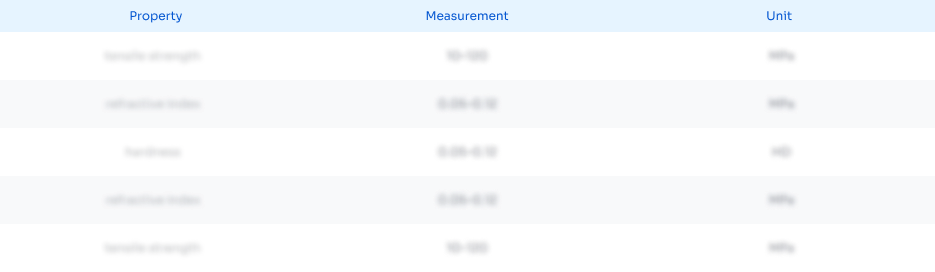
Abstract
Description
Claims
Application Information

- R&D Engineer
- R&D Manager
- IP Professional
- Industry Leading Data Capabilities
- Powerful AI technology
- Patent DNA Extraction
Browse by: Latest US Patents, China's latest patents, Technical Efficacy Thesaurus, Application Domain, Technology Topic, Popular Technical Reports.
© 2024 PatSnap. All rights reserved.Legal|Privacy policy|Modern Slavery Act Transparency Statement|Sitemap|About US| Contact US: help@patsnap.com