Soft magnetic ferrite magnetic core forming method and forming die thereof
A soft magnetic ferrite and molding method technology, which is applied in the manufacture of inductors/transformers/magnets, electrical components, circuits, etc., can solve the problems of waste of raw materials, high labor intensity of workers, and low product yield, so as to reduce scrap rate, The effect of saving labor cost
- Summary
- Abstract
- Description
- Claims
- Application Information
AI Technical Summary
Problems solved by technology
Method used
Image
Examples
Embodiment
[0017] Embodiment: A kind of soft ferrite magnetic core molding method comprises the following steps in turn: a. pressing green body, b. green body sintering and c. grinding magnetic core size:
[0018] The pressing green body: fill the raw material into the forming groove of the middle mold of the forming mold, start the pressure forming machine, and move the upper punch 1 down to the set position to pre-press the powder in the forming groove 21 of the middle mold 2. Press the set time, then the upper punch 1, the middle die 2 and the lower second punch 4 move down to the upper punch setting position, the middle die setting position and the lower second punching setting position respectively, and the back and feet of the product Press the center column to the set size and density to complete the pressing of the green body. During the pressing process of the green body, the next punch 3 is fixed, and the upper punch 1 moves downward to press against the next punch 3 to complete...
PUM
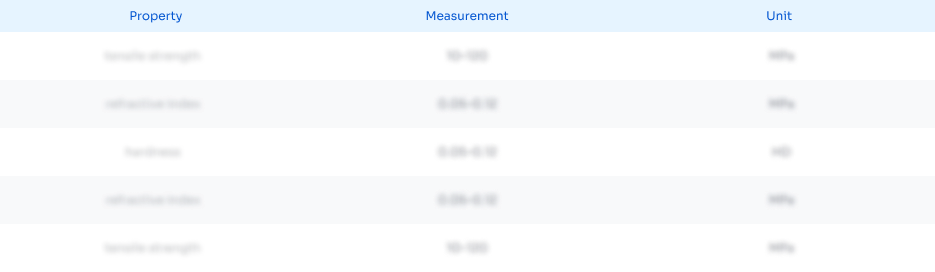
Abstract
Description
Claims
Application Information

- R&D
- Intellectual Property
- Life Sciences
- Materials
- Tech Scout
- Unparalleled Data Quality
- Higher Quality Content
- 60% Fewer Hallucinations
Browse by: Latest US Patents, China's latest patents, Technical Efficacy Thesaurus, Application Domain, Technology Topic, Popular Technical Reports.
© 2025 PatSnap. All rights reserved.Legal|Privacy policy|Modern Slavery Act Transparency Statement|Sitemap|About US| Contact US: help@patsnap.com