Permanent-magnet bias outer rotor radial AC hybrid magnetic bearing
A hybrid magnetic bearing and outer rotor technology, applied in the directions of magnetic bearings, bearings, shafts and bearings, can solve the problems of increasing the power consumption of magnetic bearings, high power amplifier cost, low power consumption, etc., to simplify the drive control method and reduce the volume. effect on cost, size reduction and cost
- Summary
- Abstract
- Description
- Claims
- Application Information
AI Technical Summary
Problems solved by technology
Method used
Image
Examples
Embodiment Construction
[0015] Such as figure 1 As shown, the present invention includes a rotor core 1 and a stator core 3, and the stator core 3 is installed in the middle of the rotor core 1, which is an outer rotor radial AC hybrid magnetic bearing structure. The stator core 3 has 6 identical stator core poles 31, 32, 33, 34, 35, 36, and these 6 identical stator core poles 31, 32, 33, 34, 35, 36 are uniform along the circumferential direction of the stator core 3 distributed, and extend outward along the radial direction of the stator core 3, and the interval angle between each stator core magnetic pole 31, 32, 33, 34, 35, 36 is 60 degrees. There is a gap of 0.3-0.6 mm between the top surfaces of the six identical stator core poles 31 , 32 , 33 , 34 , 35 , and 36 and the inner surface of the rotor core 1 . According to the requirements of the magnetic circuit, the magnetic circuit components must have good magnetic permeability, low hysteresis, and minimize eddy current loss and hysteresis loss....
PUM
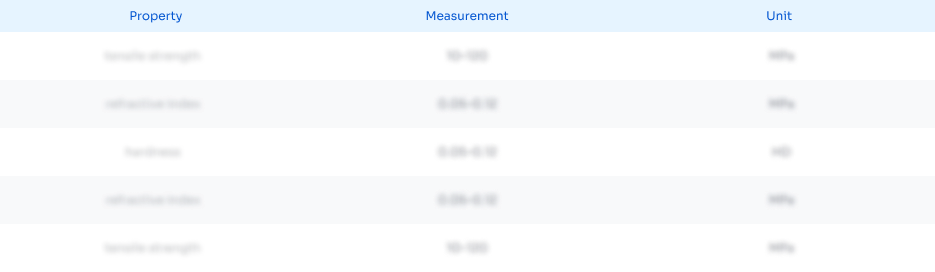
Abstract
Description
Claims
Application Information

- R&D Engineer
- R&D Manager
- IP Professional
- Industry Leading Data Capabilities
- Powerful AI technology
- Patent DNA Extraction
Browse by: Latest US Patents, China's latest patents, Technical Efficacy Thesaurus, Application Domain, Technology Topic, Popular Technical Reports.
© 2024 PatSnap. All rights reserved.Legal|Privacy policy|Modern Slavery Act Transparency Statement|Sitemap|About US| Contact US: help@patsnap.com