Method for preparing organic light-emitting diode (OLED) display screen by full printing process
A technology of electroluminescence and display screen, applied in circuits, electrical components, electrical solid devices, etc., to achieve the effect of good affinity and easy processing
- Summary
- Abstract
- Description
- Claims
- Application Information
AI Technical Summary
Problems solved by technology
Method used
Image
Examples
Embodiment 1
[0024] Such as figure 1 As shown, an organic electroluminescence display device is composed of a substrate 1 , a substrate electrode 2 , an organic functional layer 3 and a back electrode 4 sequentially stacked. The substrate 1 is a hard substrate or a flexible substrate; the substrate electrode is a transparent or translucent opaque anode, and the organic functional layer 3 includes at least a light emitting layer. Substrate (including electrodes) preparation: commercially available ITO transparent conductive glass with a pixel structure is used as the substrate 1 and the substrate electrode 2 .
[0025] Preparation of organic functional layer 3: PEDOT:PSS aqueous solution (polyaniline derivative, model 4083, purchased from Bayer, Germany) was poured on the cleaned ITO glass, and the hole injection layer was prepared by spin coating (also used as the anode Buffer layer) (film thickness 40nm at 2600rpm), and then moved into a nitrogen glove box (model NEXUS, produced by VAC, ...
Embodiment 2
[0035] Substrate (including electrodes) preparation: a commercially available ITO transparent polyethylene terephthalate (PET) film with a pixel structure is used as a substrate, which is a flexible substrate.
[0036] Preparation of organic functional layer: PEO (polyethylene oxide, molecular weight ~ 1 million, purchased from Sigma-Aldrich, USA) was dissolved in water (concentration 16 mg / ml), and PEDOT:PSS (polyaniline derivative, model 4083, (purchased from Bayer, Germany) were blended at a volume ratio of 3:2, and the hole injection layer (also used as an anode buffer layer) was prepared by screen printing (screen size 300 mesh, film formation 40-50nm). Then move into a nitrogen glove box (model NEXUS, produced by VAC Company of the United States). Heat on a hot stage at 200°C for 10 minutes. Select a high luminous efficiency green light material, a poly(phenylphenylene vinylene) derivative P-PPV, with a molecular weight of 150,000 to 300,000. The molecular structural f...
Embodiment 3
[0044] Substrate (including electrodes) preparation: commercially available IZO transparent conductive quartz with a pixel structure is used as the substrate.
[0045] Preparation of organic functional layer: PEDOT:PSS (polyaniline derivative, model 4083, purchased from Bayer, Germany) was poured on the cleaned IZO quartz, and hole injection was prepared by spin coating method (film thickness 40nm at 2600rpm) layer (also as an anode buffer layer), and then moved into a nitrogen glove box (model NEXUS, produced by VAC Corporation of the United States). Heat on a hot stage at 200°C for 10 minutes. The hole transport material PVK (polyvinylcarbazole, Sigma-Aldrich, USA) was dissolved in chlorobenzene solvent (concentration ~ 10 mg / ml). After being fully dissolved, the solution was poured on the hole injection layer, and a hole transport layer was prepared by a spin coating method (with a film thickness of 40 nm at 2000 rpm). Select high-efficiency blue light material: dendrimer...
PUM
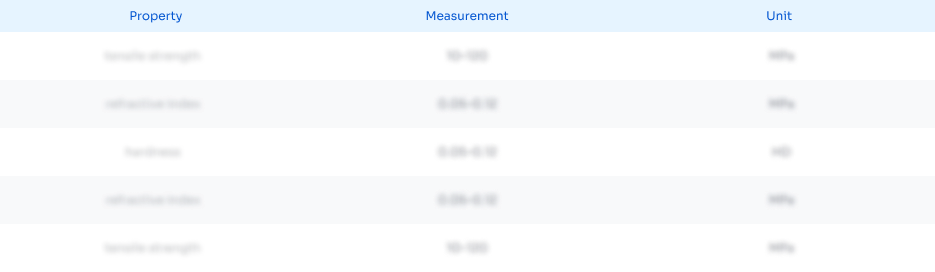
Abstract
Description
Claims
Application Information

- Generate Ideas
- Intellectual Property
- Life Sciences
- Materials
- Tech Scout
- Unparalleled Data Quality
- Higher Quality Content
- 60% Fewer Hallucinations
Browse by: Latest US Patents, China's latest patents, Technical Efficacy Thesaurus, Application Domain, Technology Topic, Popular Technical Reports.
© 2025 PatSnap. All rights reserved.Legal|Privacy policy|Modern Slavery Act Transparency Statement|Sitemap|About US| Contact US: help@patsnap.com