Process for casting U-shaped frame of wind power generation equipment
A technology of wind power generation equipment and casting technology, which is applied in the direction of manufacturing tools, casting molding equipment, metal processing equipment, etc., which can solve the problems of long solidification period in the central part, failure to arrive on time for production, unstable spheroidization level, etc., and achieve reduction Work load, fast cooling speed, effect of improving density
- Summary
- Abstract
- Description
- Claims
- Application Information
AI Technical Summary
Problems solved by technology
Method used
Examples
Embodiment Construction
[0016] A casting process for a U-shaped frame of wind power generation equipment, which is operated according to the following steps:
[0017] a) Melting, the molten iron is melted in an intermediate frequency induction furnace, and the melting temperature is controlled at 1500°C;
[0018] b), spheroidizing inoculation treatment, the spheroidizing treatment adopts a composite treatment process of 50% yttrium-based heavy rare earth nodulizer and 50% light rare earth nodulizer, and the addition of nodulizer is 1.5% of the total amount of molten iron; the inoculation treatment of molten iron The method of combining flow inoculation and instantaneous inoculation in front of the furnace is adopted. The amount of flow inoculant added is 0.6%. Instantaneous inoculant is added inoculant at the same time during the pouring process. The added amount is 0.15%. Inoculants;
[0019] c), Modeling, core making, steel pipe placement, core drop, and molding, using left and right splitting. Wh...
PUM
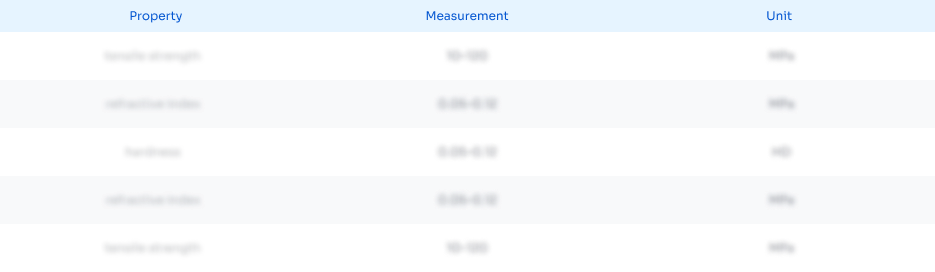
Abstract
Description
Claims
Application Information

- Generate Ideas
- Intellectual Property
- Life Sciences
- Materials
- Tech Scout
- Unparalleled Data Quality
- Higher Quality Content
- 60% Fewer Hallucinations
Browse by: Latest US Patents, China's latest patents, Technical Efficacy Thesaurus, Application Domain, Technology Topic, Popular Technical Reports.
© 2025 PatSnap. All rights reserved.Legal|Privacy policy|Modern Slavery Act Transparency Statement|Sitemap|About US| Contact US: help@patsnap.com