Production method of graphitized free-machining steel
A technology of free-cutting steel and production method, which is applied in the field of producing graphitized free-cutting steel, can solve the problems of difficulty in production and implementation, high production cost and high cooling temperature, and achieves short graphitization tempering time, low production cost, Evenly distributed effect
- Summary
- Abstract
- Description
- Claims
- Application Information
AI Technical Summary
Problems solved by technology
Method used
Image
Examples
Embodiment 1
[0026] A kind of production method of graphitized free-cutting steel, its step:
[0027] 1) The main chemical composition and weight percentage are: 0.453%C, 1.70%Si, 1.5%Al, 0.34%Mn, <0.020%P, <0.035%S, and the balance is Fe and the slab is heated to 1200-1205°C;
[0028] 2) Carry out heat preservation: heat preservation at a temperature of 1200-1205°C for 60 minutes;
[0029] 3) Cooling: cooling the slab to 1050-1060°C at a cooling rate of 10°C / s;
[0030] 4) Rough rolling: 3 times of rough rolling at 1050-1060°C, controlling the reduction ratio of each pass at 20%;
[0031] 5) Cooling: After rough rolling, cool the rough rolled plate to 850-855°C at a cooling rate of 5°C / s;
[0032] 6) Finish rolling: carry out finish rolling according to 4 passes, control the interval time of each pass for 2.5 seconds, and the deformation amount of each pass is 10%;
[0033] 7) Air cooling: the air cooling time is 30 seconds;
[0034] 8) Perform rapid water cooling: cool to room temper...
Embodiment 2
[0038] A kind of production method of graphitized free-cutting steel, its step:
[0039] 1) The main chemical composition and weight percentage are: 0.43%C, 1.50%Si, 0.005%B, 0.45%Mn, 0.009%P, 0.010%S, and the balance is Fe and the slab is heated to 1210-1215°C;
[0040] 2) Keep warm: keep warm for 80 minutes at a temperature of 1210-1215°C;
[0041] 3) Cooling: cooling the billet to 1070-1075°C at a cooling rate of 12°C / s;
[0042] 4) Rough rolling: carry out 5 times of rough rolling at 1070-1075°C, and control the reduction ratio of each pass at 26%;
[0043] 5) Cooling: After rough rolling, cool the rough rolled plate to 880-885°C at a cooling rate of 8°C / s;
[0044] 6) Carry out finish rolling: carry out finish rolling according to 5 passes, control the interval time of each pass for 2 seconds, and the deformation amount of each pass is 25%;
[0045] 7) Air cooling: the air cooling time is 40 seconds;
[0046] 8) Rapid water cooling: cooling to room temperature at a co...
Embodiment 3
[0050] A kind of production method of graphitized free-cutting steel, its step:
[0051] 1) The main chemical composition and weight percentage are: C: 0.62%, Si: 0.95%, Al: 0.05%, Mn: 0.80%, P: 0.0176%, S: 0.182%, Zr: 0.15%, Nb: 0.1% , the billet with the balance being Fe is heated to 1225-1230°C;
[0052] 2) Keep warm: keep warm for 100 minutes at a temperature of 1225-1230°C;
[0053] 3) Cooling: cooling the billet to 1090-1097°C at a cooling rate of 15°C / s;
[0054]4) Rough rolling: carry out 6 times of rough rolling at 1090-1097°C, and control the reduction ratio of each pass at 32%;
[0055] 5) Cooling: After rough rolling, cool the rough rolled plate to 900-910°C at a cooling rate of 12°C / s;
[0056] 6) Finish rolling: carry out finish rolling according to 6 passes, control the interval time of each pass to 2.8 seconds, and the deformation amount of each pass is 35%;
[0057] 7) Air cooling: the air cooling time is 75 seconds;
[0058] 8) Perform rapid water coolin...
PUM
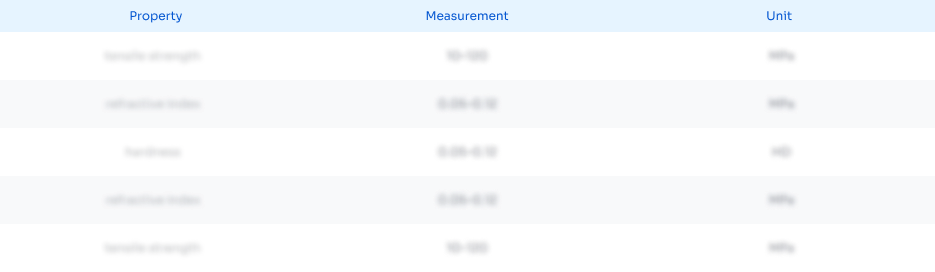
Abstract
Description
Claims
Application Information

- R&D
- Intellectual Property
- Life Sciences
- Materials
- Tech Scout
- Unparalleled Data Quality
- Higher Quality Content
- 60% Fewer Hallucinations
Browse by: Latest US Patents, China's latest patents, Technical Efficacy Thesaurus, Application Domain, Technology Topic, Popular Technical Reports.
© 2025 PatSnap. All rights reserved.Legal|Privacy policy|Modern Slavery Act Transparency Statement|Sitemap|About US| Contact US: help@patsnap.com