Method for producing mercury-free alkaline manganese electrolytic manganese dioxide
A technology of electrolytic manganese dioxide and production methods, applied in the direction of electrolysis process, electrolysis components, improvement of process efficiency, etc., can solve the problems of long turnaround time, low leaching rate, long process flow, etc., and achieve good economic and social benefits , reduce production costs, and shorten the process flow
- Summary
- Abstract
- Description
- Claims
- Application Information
AI Technical Summary
Problems solved by technology
Method used
Image
Examples
Embodiment 1
[0016] Mix manganese oxide ore powder containing 14.32% of manganese and pyrite powder with sulfur content of 44.54% at a dry ratio of 1:0.24, add water to 98% sulfuric acid to prepare a 100g / L dilute sulfuric acid solution, mix The final manganese oxide powder and pyrite powder and the prepared sulfuric acid are continuously added into the continuous leaching tank at the same time according to the ratio of 1:0.47, and are stirred continuously at the same time. The continuous leaching tank is composed of one leaching tank to form a one-stage continuous process. Leaching, the effective volume of the leaching tank is 1m 3 , the tank temperature is 95°C, the leaching reaction time is 3 hours from feeding to the material liquid coming out of the leaching tank, and when the pH value reaches 3 to 3.5, it indicates that the leaching reaction has been completed. Stir continuously during the reaction, and the material liquid flowing out of the leaching tank Enter the neutralization tan...
Embodiment 2
[0019] Mix manganese oxide ore powder containing 15.56% of manganese and pyrite powder with sulfur content of 40.54% according to the dry specific gravity of 1:0.24, add water to 98% sulfuric acid to prepare a 100g / L dilute sulfuric acid solution, mix The final manganese oxide powder and pyrite powder and the prepared sulfuric acid are continuously added into the continuous leaching tank at the same time according to the ratio of 1:0.47, and are stirred continuously at the same time. The continuous leaching tank is composed of three leaching tanks connected in series to form three Level continuous leaching, the effective volume of each leaching tank is 1m 3 , the material liquid enters the second-level leaching tank and then enters the third-level leaching tank. The temperature of each tank is 93°C. The leaching reaction time from feeding to the material liquid coming out of the third-level leaching tank is 3.5 hours. Stir continuously during the reaction , the feed liquid flo...
Embodiment 3
[0022] Mix manganese oxide ore powder containing 13.58% of manganese and pyrite powder with sulfur content of 47.44% according to the dry ratio of 1:0.24, add water to 98% sulfuric acid to prepare a 100g / L dilute sulfuric acid solution, mix The final manganese oxide powder and pyrite powder and the prepared sulfuric acid are continuously added into the continuous leaching tank at the ratio of 1:0.47 at the same time, and are stirred continuously at the same time. The continuous leaching tank is composed of seven leaching tanks connected in series to form seven leaching tanks. Level continuous leaching, the effective volume of each leaching tank is 1m 3, the feed liquid enters the second stage leaching tank and then enters the third to seventh stage leaching tanks. The temperature of each tank is 95°C. The leaching reaction time from feeding to feed liquid coming out of the seventh stage leaching tank is 4 hours. The reaction process Stirring continuously in the middle, the mat...
PUM
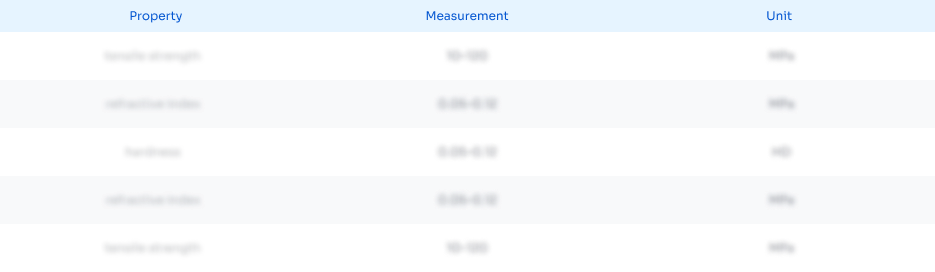
Abstract
Description
Claims
Application Information

- R&D
- Intellectual Property
- Life Sciences
- Materials
- Tech Scout
- Unparalleled Data Quality
- Higher Quality Content
- 60% Fewer Hallucinations
Browse by: Latest US Patents, China's latest patents, Technical Efficacy Thesaurus, Application Domain, Technology Topic, Popular Technical Reports.
© 2025 PatSnap. All rights reserved.Legal|Privacy policy|Modern Slavery Act Transparency Statement|Sitemap|About US| Contact US: help@patsnap.com