All-backheating drainage system of heat supply network heater for supercritical concurrent boiler thermal power plant
A heating network heater and once-through boiler technology, applied in lighting and heating equipment, preheating, supplementary water supply, etc., can solve problems such as difficulty in ensuring the quality of boiler feed water, heat loss from heating network heater drainage, and boiler safety impacts, etc.
- Summary
- Abstract
- Description
- Claims
- Application Information
AI Technical Summary
Problems solved by technology
Method used
Image
Examples
Embodiment Construction
[0027] In order to enable the examiner to understand the system composition and implementation of the present invention, the description is as follows in conjunction with the drawings:
[0028] The water-repellent mode of the heat network heater of the present invention is as follows: Figure 4 and Figure 5 As shown, the condenser 3 is connected to the shaft seal cooler 7 of the condensate system, the outlet end of the shaft seal cooler 7 of the condensate system is connected to the water inlet end of the condensate polishing equipment 6, and the heating network heater 1 is connected to the drain cooling The water inlet A of the drain cooler 5 is connected, the outlet B of the drain cooler 5 is connected with the outlet E of the shaft seal cooler of the condensate system, and the heat exchange inlet C of the drain cooler 5 is connected with the outlet of the condensate polishing equipment F is connected, and the heat exchange outlet D of the hydrophobic cooler 5 is connected...
PUM
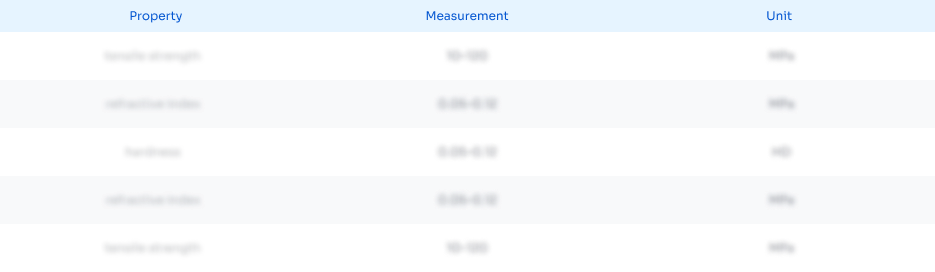
Abstract
Description
Claims
Application Information

- Generate Ideas
- Intellectual Property
- Life Sciences
- Materials
- Tech Scout
- Unparalleled Data Quality
- Higher Quality Content
- 60% Fewer Hallucinations
Browse by: Latest US Patents, China's latest patents, Technical Efficacy Thesaurus, Application Domain, Technology Topic, Popular Technical Reports.
© 2025 PatSnap. All rights reserved.Legal|Privacy policy|Modern Slavery Act Transparency Statement|Sitemap|About US| Contact US: help@patsnap.com