Production method of fabric for gas bag
A production method and fabric technology, applied in the direction of fabrics, textiles, looms, etc., can solve the problems that cannot meet the development requirements of the automobile industry, reduce production efficiency, and complex loom structures, etc., and achieve high energy absorption and low air permeability , the effect of low initial modulus
- Summary
- Abstract
- Description
- Claims
- Application Information
AI Technical Summary
Problems solved by technology
Method used
Image
Examples
Embodiment 1
[0029] The warp and weft yarns are all made of nylon 66 filaments with a total fineness of 350dtex, a number of 136, and a circular cross section. Water-jet loom is used to weave plain weave, and a yarn pressing bar is added under the sheet warp between the heald frame of the loom and the back beam of the loom. Wherein, the specific position of the yarn pressing rod is that the horizontal position is located at 40 cm away from the back beam; the upward pressing displacement is 4 cm away from the warp position line. A fabric with a warp density of 59 threads / inch and a weft density of 59 threads / inch was obtained. The physical properties of the obtained fabrics were evaluated, and the relevant physical properties are shown in Table 1.
Embodiment 2
[0031] The warp and weft yarns are all made of nylon 66 filaments with a total fineness of 350dtex, a number of 136, and a circular cross section. Water-jet loom is used to weave plain weave, and a yarn pressing bar is added under the sheet warp between the heald frame of the loom and the back beam of the loom. Wherein, the specific position of the yarn pressing rod is that the horizontal position is located at 45 cm away from the back beam; the upward pressing displacement is at 6 cm away from the warp position line. A fabric with a warp density of 59 threads / inch and a weft density of 59 threads / inch was obtained. The physical properties of the obtained fabrics were evaluated, and the relevant physical properties are shown in Table 1.
PUM
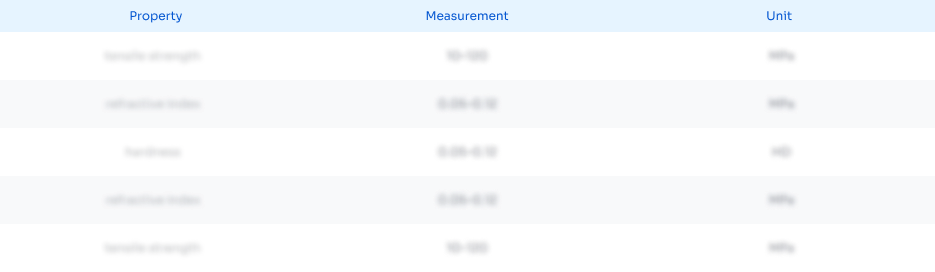
Abstract
Description
Claims
Application Information

- Generate Ideas
- Intellectual Property
- Life Sciences
- Materials
- Tech Scout
- Unparalleled Data Quality
- Higher Quality Content
- 60% Fewer Hallucinations
Browse by: Latest US Patents, China's latest patents, Technical Efficacy Thesaurus, Application Domain, Technology Topic, Popular Technical Reports.
© 2025 PatSnap. All rights reserved.Legal|Privacy policy|Modern Slavery Act Transparency Statement|Sitemap|About US| Contact US: help@patsnap.com