Gear blank isothermal annealing process and isothermal annealing production line
A technology of isothermal annealing and process curve, which is applied to the improvement of process efficiency, manufacturing tools, furnace types, etc., to achieve the effects of reducing heat loss, prolonging the service life of the furnace, and saving energy.
- Summary
- Abstract
- Description
- Claims
- Application Information
AI Technical Summary
Problems solved by technology
Method used
Image
Examples
Embodiment Construction
[0016] The following is attached Figure 4 with attached Figure 6 The specific implementation of the present invention is described in detail.
[0017] attached Figure 4 It is a schematic diagram of the forging preheating isothermal annealing process curve of the present invention. According to this process requirement, after the gear blank is released from the die forging hammer, the blank can be sent into the Figure 6 In the mesh belt type soaking furnace, the soaking temperature is selected according to the TTT curve of the forging billet steel type. After equalizing, the blank will automatically fall to the working area of the intermediate frequency heating furnace. At this time, the blank is loaded into the intermediate frequency sensor by manual or automatic loading machine Inside, the intermediate frequency heating program is started, and the heating is stopped after heating to the predetermined austenitizing temperature. The gear blank is sent into the mesh belt...
PUM
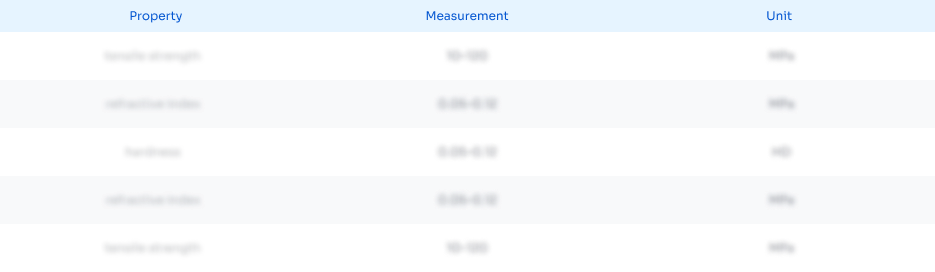
Abstract
Description
Claims
Application Information

- R&D
- Intellectual Property
- Life Sciences
- Materials
- Tech Scout
- Unparalleled Data Quality
- Higher Quality Content
- 60% Fewer Hallucinations
Browse by: Latest US Patents, China's latest patents, Technical Efficacy Thesaurus, Application Domain, Technology Topic, Popular Technical Reports.
© 2025 PatSnap. All rights reserved.Legal|Privacy policy|Modern Slavery Act Transparency Statement|Sitemap|About US| Contact US: help@patsnap.com