System and method for recovering waste heat of continuous hot steel slag
A waste heat recovery system and technology of hot steel slag, applied in the field of waste heat recovery, can solve the problems of low energy consumption heat recovery process of hot steel slag, high fluidity requirements of steel slag, low heat recovery rate and service life, etc., to achieve continuous and stable recovery of heat, Adjustable steel slag conveying volume and the effect of processing volume control
- Summary
- Abstract
- Description
- Claims
- Application Information
AI Technical Summary
Problems solved by technology
Method used
Image
Examples
Embodiment Construction
[0028] like figure 1 As shown in the figure, the steel slag dumped from the slag tank with a temperature higher than 1500 ℃ enters the slag removal device from the slag receiving hopper, and is continuously conveyed in the slag removal device and transported to the rotary drum. At the same time, air is blown into the slag removal device and the rotary drum through the fan to achieve secondary heat exchange with the steel slag, so that the steel slag is lowered to below 700°C and 300°C respectively, the air is heated and converted into hot air, and water is generated through the waste heat boiler. The steam is used for energy utilization, and the heat exchange is transformed into a cold state and the steel slag broken by the rotary drum is discharged from the slag outlet.
[0029] like figure 2 As shown, the key equipment slag removal device in this process system adopts a tunnel structure. The hot steel slag in the slag tank enters the slag removal device through the slag i...
PUM
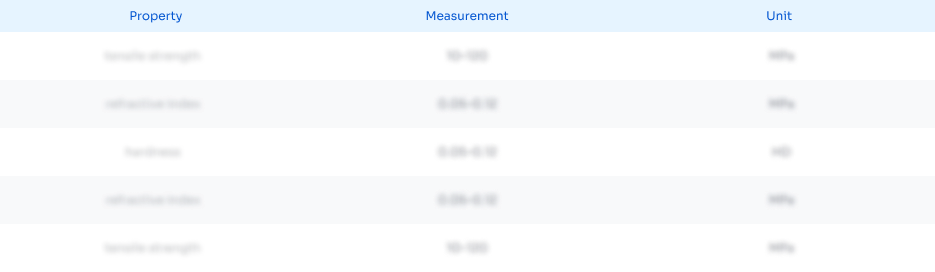
Abstract
Description
Claims
Application Information

- R&D
- Intellectual Property
- Life Sciences
- Materials
- Tech Scout
- Unparalleled Data Quality
- Higher Quality Content
- 60% Fewer Hallucinations
Browse by: Latest US Patents, China's latest patents, Technical Efficacy Thesaurus, Application Domain, Technology Topic, Popular Technical Reports.
© 2025 PatSnap. All rights reserved.Legal|Privacy policy|Modern Slavery Act Transparency Statement|Sitemap|About US| Contact US: help@patsnap.com