LED lead frame and electroplating method and electroplating equipment thereof
A lead frame, selective electroplating technology, applied in the direction of circuits, electrical components, semiconductor devices, etc., can solve the problems of affecting the quality of LED products, high production costs, low silver utilization, etc., to reduce the area of electroplated silver layer and high production costs , The effect of reducing the cost of electroplating
- Summary
- Abstract
- Description
- Claims
- Application Information
AI Technical Summary
Problems solved by technology
Method used
Image
Examples
Embodiment Construction
[0066] see Figure 5 to Figure 7 Shown is an LED lead frame 10 disclosed by the present invention, which is divided into three parts: a frame 11 , a functional area 12 and a chip placement area 13 . An anti-substitution protective film 14 is formed on the entire lead frame 10 . The primary silver plating layer 15 is formed on the entire functional area 12 through selective electroplating with silver. On the chip placement area 13, form secondary silver-plated layer 16 through partial electroplating silver again, make the silver-plated layer of chip placement area 13 (comprising silver-plated layer 15 and secondary silver-plated layer 16) than the silver-plated layer of surrounding functional area 12 layer (only one silver plating layer 15) is thick. An anti-copper oxidation organic protective film 17 is formed on the frame 11 .
[0067] Such as Figure 8 Shown, be the electroplating method of the LED lead frame that the present invention prompts, technological process is a...
PUM
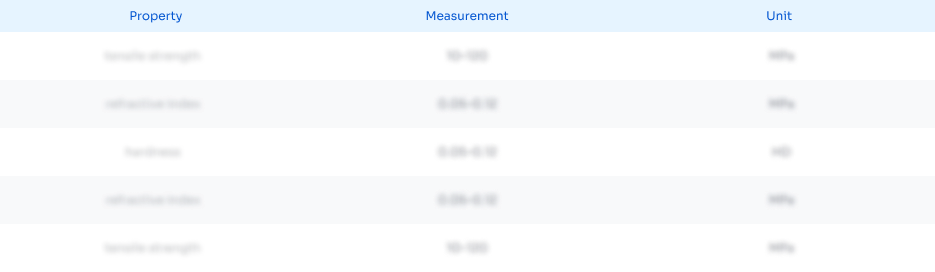
Abstract
Description
Claims
Application Information

- R&D
- Intellectual Property
- Life Sciences
- Materials
- Tech Scout
- Unparalleled Data Quality
- Higher Quality Content
- 60% Fewer Hallucinations
Browse by: Latest US Patents, China's latest patents, Technical Efficacy Thesaurus, Application Domain, Technology Topic, Popular Technical Reports.
© 2025 PatSnap. All rights reserved.Legal|Privacy policy|Modern Slavery Act Transparency Statement|Sitemap|About US| Contact US: help@patsnap.com