Preparation method of polybutylene terephthalate/adipate butanediol copolyester
A technology of polybutylene terephthalate and butylene diacid copolyester, which is applied in the field of polyester synthesis, can solve problems such as adverse effects on product quality, and achieve shortened synthesis reaction time, improved reaction speed, and high performance characteristics. The effect of viscosity
- Summary
- Abstract
- Description
- Claims
- Application Information
AI Technical Summary
Problems solved by technology
Method used
Image
Examples
Embodiment 1
[0027] Into a 5 L stainless steel reaction kettle equipped with nitrogen inlet, condensate outlet and stirrer, 820 g of terephthalic acid (PTA), 180 g of adipic acid (AA) and 383 g of 1,4-butanediol (1,4-BD ), 0.2g tetrabutyl titanate (equivalent to 200ppm of the total weight of PTA and AA), 0.6g antimony acetate (equivalent to 600ppm of the total weight of PTA and AA). Maintain normal pressure in the kettle and stir at a constant speed. When the temperature in the reaction kettle rises to 150°C, water will start to come out. Continue to raise the temperature and control the inner temperature of the reaction kettle to not exceed 220°C. When the amount of water is produced, the esterification reaction ends. Continue to add 0.05g trimethyl phosphate (50ppm equivalent to the total weight of PTA and AA) in the kettle, vacuumize, make the pressure in the polymerization kettle be reduced to below 150Pa in 60 minutes, react under this pressure for 85 minutes, react The final tempera...
Embodiment 2
[0033]Into a 5 L stainless steel reaction kettle equipped with nitrogen inlet, condensate outlet and stirrer, 630 g of terephthalic acid (PTA), 370 g of adipic acid (AA) and 686 g of 1,4-butanediol (1,4-BD ), 0.2g tetrapropyl titanate (equivalent to 200ppm of the total weight of PTA and AA) and 0.3g antimony trioxide (equivalent to 300ppm of the total weight of PTA and AA). Maintain normal pressure in the kettle and stir at a constant speed. When the temperature in the reaction kettle rises to 150°C, water will start to come out. Continue to raise the temperature and control the inner temperature of the reaction kettle to not exceed 220°C. When the amount of water is produced, the esterification reaction ends. Continue to add 0.3g tetrapropyl titanate (equivalent to 300ppm of the total weight of PTA and AA), 0.1g antimony trioxide (equivalent to 100ppm of the total weight of PTA and AA) and 0.15g trimethyl phosphate (equivalent to 100ppm of the total weight of PTA and AA) in t...
Embodiment 3
[0035] Into a 5 L stainless steel reaction kettle equipped with nitrogen inlet, condensate outlet and stirrer, 532 g of terephthalic acid (PTA), 468 g of adipic acid (AA) and 806 g of 1,4-butanediol (1,4-BD ), 0.3g tetramethyl titanate (equivalent to 300ppm of the total weight of PTA and AA) and 0.3g antimony ethylene glycol (equivalent to 300ppm of the total weight of PTA and AA). Maintain normal pressure in the kettle and stir at a constant speed. When the temperature in the reaction kettle rises to 150°C, water will start to come out. Continue to raise the temperature and control the inner temperature of the reaction kettle to not exceed 220°C. When the amount of water is produced, the esterification reaction ends. Continue to add 0.5g tetramethyl titanate (equivalent to 500ppm of the total weight of PTA and AA) and 0.2g triphenyl phosphate (equivalent to 200ppm of the total weight of PTA and AA) in the kettle, and vacuumize to make the polymerization kettle The pressure i...
PUM
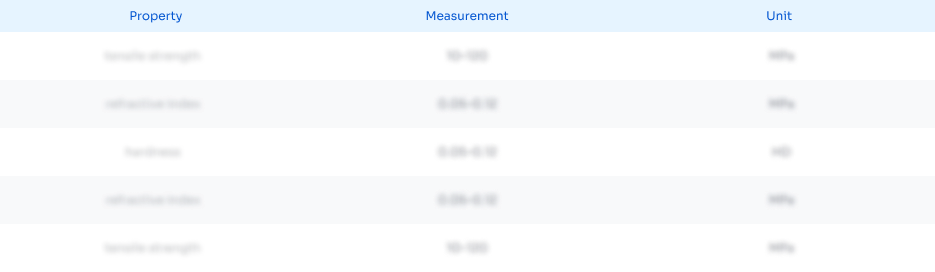
Abstract
Description
Claims
Application Information

- R&D
- Intellectual Property
- Life Sciences
- Materials
- Tech Scout
- Unparalleled Data Quality
- Higher Quality Content
- 60% Fewer Hallucinations
Browse by: Latest US Patents, China's latest patents, Technical Efficacy Thesaurus, Application Domain, Technology Topic, Popular Technical Reports.
© 2025 PatSnap. All rights reserved.Legal|Privacy policy|Modern Slavery Act Transparency Statement|Sitemap|About US| Contact US: help@patsnap.com