On rust paint and preparation method thereof
A technology of rusty coatings and resins, applied in anti-corrosion coatings, epoxy resin coatings, coatings, etc., can solve the problems of limited rust treatment capacity, narrow application range, and limited anti-rust ability, so as to achieve good sealing effect and improve Good effect of cross-linking density and sealability
- Summary
- Abstract
- Description
- Claims
- Application Information
AI Technical Summary
Problems solved by technology
Method used
Examples
preparation example Construction
[0030] The present invention also provides a preparation method for preparing the above-mentioned rusty paint, including:
[0031] To prepare the resin component: take 45 to 60 parts of chelating resin, 10 to 30 parts of benzyl alcohol and 25 to 35 parts of diluent and mix them and disperse them evenly;
[0032] Preparation of curing agent components: Take 80 to 90 parts of ketimine modified fatty amine epoxy resin curing agent, 4 to 10 parts of epoxy resin accelerator and 5 to 10 parts of benzyl alcohol and mix them and disperse them evenly ;
[0033] The resin component and the curing agent component are mixed in a weight ratio of 3 to 4: 1 to obtain an epoxy resin coating.
Embodiment 1
[0036] To prepare the resin component: take 49.3kg of chelating resin, 25kg of benzyl alcohol and 25.7kg of diluent and mix them and disperse them evenly in a disperser;
[0037] Preparation of curing agent components: take 82.5kg of ketimine modified fatty amine epoxy resin curing agent, 8kg of 2,4,6-triphenol and 9.5kg of benzyl alcohol and mix them and disperse them evenly in a disperser;
[0038] Before use, the resin component and the curing agent component are mixed according to a weight ratio of 3.5:1 to obtain an epoxy resin coating.
Embodiment 2
[0040] To prepare the resin component: take 55kg of chelating resin, 18.5 benzyl alcohol and 26.5kg of diluent and mix them and disperse them evenly in a disperser;
[0041] Preparation of curing agent components: take 89.5 kg of ketimine modified fatty amine epoxy resin curing agent, 5.5 kg of 2,4,6-tris (dimethylaminomethyl) phenol and 5.0 kg of benzyl alcohol and mix them before dispersing Evenly dispersed in the machine;
[0042] Before use, the resin component and the curing agent component are mixed in a weight ratio of 3.2:1 to obtain an epoxy resin coating.
PUM
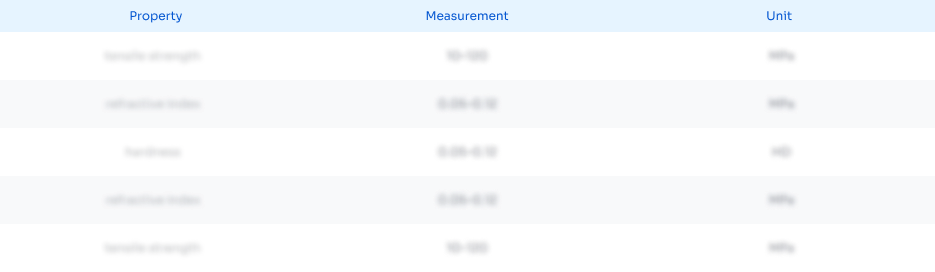
Abstract
Description
Claims
Application Information

- R&D
- Intellectual Property
- Life Sciences
- Materials
- Tech Scout
- Unparalleled Data Quality
- Higher Quality Content
- 60% Fewer Hallucinations
Browse by: Latest US Patents, China's latest patents, Technical Efficacy Thesaurus, Application Domain, Technology Topic, Popular Technical Reports.
© 2025 PatSnap. All rights reserved.Legal|Privacy policy|Modern Slavery Act Transparency Statement|Sitemap|About US| Contact US: help@patsnap.com