System for recycling SO2 and NO from oxygen-enriched combustion boiler fume CO2 collection
A boiler flue gas, oxygen-enriched combustion technology, applied in the direction of climate sustainability, air quality improvement, direct carbon dioxide emission reduction, etc. Power consumption and dehydration power consumption, eliminating desulfurization and denitrification devices, and improving combustion and heat transfer efficiency
- Summary
- Abstract
- Description
- Claims
- Application Information
AI Technical Summary
Problems solved by technology
Method used
Image
Examples
Embodiment Construction
[0030] The invention provides a CO 2 Recovery of SO from capture 2 With NO system, the present invention will be further described below in conjunction with the accompanying drawings and specific embodiments.
[0031] Such as figure 1 As shown, the exhaust port of the boiler 2 is connected to the first cooler 3, and then connected with the primary compressor 4, the second cooler 5, the first contact tower 6, the secondary compressor 7, the third cooler 8, The second contact tower 9 and the carbon dioxide compression and condensation device 10 are connected in sequence.
[0032] The working process of the system is: after the oxygen produced in the air separation device 1 is mixed with the recirculated flue gas in a certain proportion, they are sent to the furnace of the boiler 2 together with pulverized coal for combustion, and the burned boiler exhaust smoke passes through the first cooler 3 Cool to 30°C and send it to the primary compressor 4 Pressurize to 1.5-2MPa. The ...
PUM
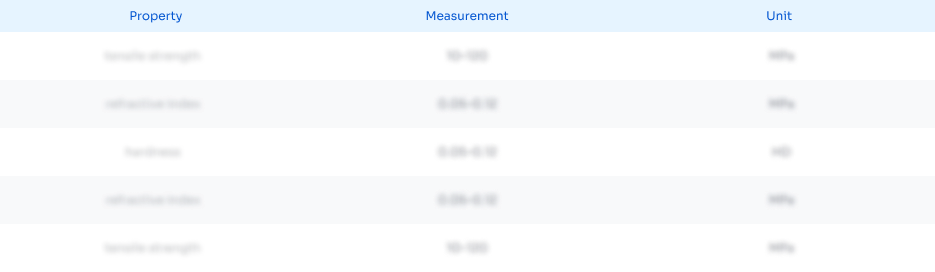
Abstract
Description
Claims
Application Information

- R&D
- Intellectual Property
- Life Sciences
- Materials
- Tech Scout
- Unparalleled Data Quality
- Higher Quality Content
- 60% Fewer Hallucinations
Browse by: Latest US Patents, China's latest patents, Technical Efficacy Thesaurus, Application Domain, Technology Topic, Popular Technical Reports.
© 2025 PatSnap. All rights reserved.Legal|Privacy policy|Modern Slavery Act Transparency Statement|Sitemap|About US| Contact US: help@patsnap.com