Alkali-hydrogen peroxide method-based cooking catalyst and clean pulping process
A hydrogen peroxide method and hydrogen peroxide technology, applied in the field of papermaking, can solve problems such as high cost, complicated process, and failure to meet emission requirements, and achieve the effects of simple operation, easy modularization, and easy recycling
- Summary
- Abstract
- Description
- Claims
- Application Information
AI Technical Summary
Problems solved by technology
Method used
Image
Examples
Embodiment 1
[0018] A cooking catalyst based on the alkali-hydrogen peroxide method, consisting of 3 kg of chelating agent EDTA, 4 kg of magnesium sulfate, 7 kg of sodium silicate, 16 kg of urea, and 25 kg of sulfamic acid.
[0019] The clean pulping process based on the alkali-hydrogen peroxide method, as shown in Figure 1, includes:
[0020] 1) The fiber raw material is subjected to pretreatment operations of cutting grass, dust removal, and water washing. The washing water removes solid impurities and then returns to the washing equipment for reuse. The solid impurities separated from the washing water are used to make fertilizer.
[0021] 2) Alkali-hydrogen peroxide cooking of the pretreated fiber material: cooking liquor ratio 1:3, add 260kg NaOH, 150kg hydrogen peroxide (concentration 30wt%), and the above cooking catalyst, normal temperature and pressure Cook for 2.5 hours.
[0022] 3) Squeeze the slurry after the cooking, the obtained cooking residue is white liquor. After removing the sol...
Embodiment 2
[0025] A cooking catalyst based on the alkali-hydrogen peroxide method, consisting of 5 kg of chelating agent DTPA, 5 kg of magnesium sulfate, 10 kg of sodium silicate, 20 kg of urea, and 32 kg of sulfamic acid.
[0026] The clean pulping process based on the alkali-hydrogen peroxide method, as shown in Figure 1, includes:
[0027] 1) The fiber raw material is subjected to pretreatment operations of cutting grass, dust removal, and water washing. The washing water removes solid impurities and then returns to the washing equipment for reuse. The solid impurities separated from the washing water are used to make fertilizer.
[0028] 2) Alkali-hydrogen peroxide cooking on the pretreated fiber material: cooking liquor ratio 1:5, adding 280kg NaOH, 190kg hydrogen peroxide (concentration 30wt%), and the above-mentioned cooking catalyst, cooking temperature control At 50°C, 50 minutes each time.
[0029] 3) Squeeze the slurry after the cooking, the obtained cooking residue is white liquor. A...
Embodiment 3
[0032] A cooking catalyst based on the alkali-hydrogen peroxide method, consisting of chelating agent TMA-528kg, magnesium sulfate 8kg, sodium silicate 12kg, urea 25kg, and sulfamic acid 40kg.
[0033] The clean pulping process based on the alkali-hydrogen peroxide method, as shown in Figure 1, includes:
[0034] 1) The fiber raw material is subjected to pretreatment operations of cutting grass, dust removal, and water washing. The washing water removes solid impurities and then returns to the washing equipment for reuse. The solid impurities separated from the washing water are used to make fertilizer.
[0035] 2) Alkali-hydrogen peroxide cooking of the pretreated fiber material: cooking liquor ratio 1:8, add 320kg of NaOH, 260kg of hydrogen peroxide (calculated at a concentration of 30wt%) and the above-mentioned cooking catalyst per absolute dry pulp. The cooking temperature is controlled at 100°C, 90 minutes each time.
[0036] 3) Squeeze the slurry after the cooking, the obtained...
PUM
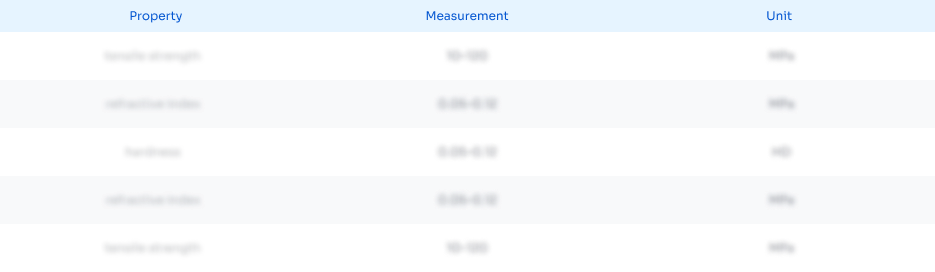
Abstract
Description
Claims
Application Information

- R&D
- Intellectual Property
- Life Sciences
- Materials
- Tech Scout
- Unparalleled Data Quality
- Higher Quality Content
- 60% Fewer Hallucinations
Browse by: Latest US Patents, China's latest patents, Technical Efficacy Thesaurus, Application Domain, Technology Topic, Popular Technical Reports.
© 2025 PatSnap. All rights reserved.Legal|Privacy policy|Modern Slavery Act Transparency Statement|Sitemap|About US| Contact US: help@patsnap.com