Recycling method of carbide slag
A processing method and technology for carbide slag, applied in cement production and other directions, can solve the problems of low product added value, difficult to consume carbide slag, and economic benefits are not obvious, and achieve high product added value, good economic benefits, and less equipment investment. Effect
- Summary
- Abstract
- Description
- Claims
- Application Information
AI Technical Summary
Problems solved by technology
Method used
Examples
Embodiment 1
[0031] A resourceful treatment method for carbide slag, the treatment method comprising the following steps:
[0032] (1) Add 100g of calcium carbide slag with a water content of 20% to a 1000mL four-neck flask equipped with a stirrer, reflux condenser and constant pressure funnel, then add 68g of water and 422g of sodium carbonate solution with a concentration of 13.3% by weight, and After stirring and reacting at 90°C for 1 hour, cool and filter to obtain bright yellow filtrate B and off-white filter residue A. The obtained filtrate B is caustic soda solution. g activated carbon, stirred and decolorized for 0.5 hour under micro-boiling conditions, cooled and filtered to obtain a colorless and transparent filtrate, then evaporated and concentrated under normal pressure to obtain 146g of colorless and transparent 30% caustic soda, and the waste activated carbon was mixed as fuel for incineration;
[0033] (2) Add filter residue A to a 1000mL four-neck flask equipped with a sti...
Embodiment 2
[0036] A resourceful treatment method for carbide slag, the treatment method comprising the following steps:
[0037] (1) Add 100g of calcium carbide slag with a water content of 20% to a 2000mL four-neck flask equipped with a stirrer, reflux condenser and constant pressure funnel, then add 68g of water and 1125g of sodium carbonate solution with a concentration of 5% by weight, and After stirring and reacting at 70°C for 2 hours, cool and filter to obtain bright yellow filtrate B and off-white filter residue A. The obtained filtrate B is caustic soda solution. g of activated carbon, stirred and decolorized for 0.5 hours under micro-boiling conditions, cooled and filtered to obtain a colorless and transparent filtrate, and then evaporated and concentrated under normal pressure to obtain 147.5g of colorless and transparent 30% caustic soda, and waste activated carbon was mixed as fuel for incineration. ;
[0038] (2) Add filter residue A to a 1000mL four-neck flask equipped wi...
Embodiment 3
[0041] A resourceful treatment method for carbide slag, the treatment method comprising the following steps:
[0042] (1) Add 200g of calcium carbide slag with a water content of 20% to a 2000mL four-neck flask equipped with a stirrer, reflux condenser and constant pressure funnel, then add 136g of water and 375g of sodium carbonate solution with a concentration of 30% by weight, and After stirring and reacting at 95°C for 0.5 hours, cool and filter to obtain bright yellow filtrate B and off-white filter residue A. The resulting filtrate B is caustic soda solution. g of activated carbon, stirred and decolorized for 0.5 hours under micro-boiling conditions, cooled and filtered to obtain a colorless and transparent filtrate, and then evaporated and concentrated under normal pressure to obtain 287.5g of colorless and transparent 30% caustic soda, and waste activated carbon was mixed as fuel for incineration. ;
[0043] (2) Add filter residue A to a 3000mL four-neck flask equippe...
PUM
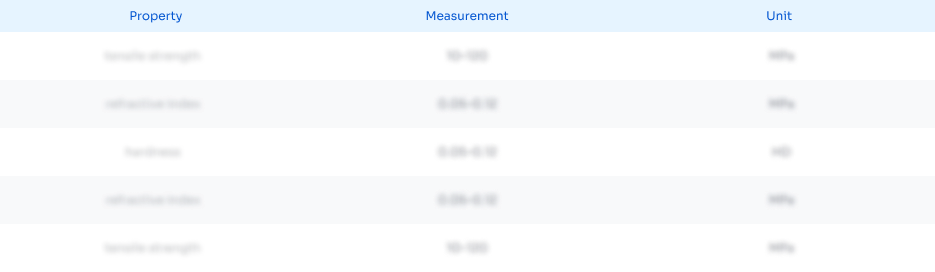
Abstract
Description
Claims
Application Information

- Generate Ideas
- Intellectual Property
- Life Sciences
- Materials
- Tech Scout
- Unparalleled Data Quality
- Higher Quality Content
- 60% Fewer Hallucinations
Browse by: Latest US Patents, China's latest patents, Technical Efficacy Thesaurus, Application Domain, Technology Topic, Popular Technical Reports.
© 2025 PatSnap. All rights reserved.Legal|Privacy policy|Modern Slavery Act Transparency Statement|Sitemap|About US| Contact US: help@patsnap.com