Method for preparing manganese sulfate from sulfur-containing waste residue
A manganese sulfate and waste slag technology, which is applied to the removal of manganese sulfate and solid waste, can solve the problems of large environmental pollution, environmental pollution, and high utilization costs, and achieve outstanding environmental benefits, significant economic benefits, and reduced production costs.
- Summary
- Abstract
- Description
- Claims
- Application Information
AI Technical Summary
Problems solved by technology
Method used
Examples
Embodiment 1
[0012] Mix acid leaching electrolytic manganese slag and lead-zinc tailings at a ratio of 3.5:1, and add a small amount of diaspore and iron powder, so that the mass percentages of various oxides in the mixture are: CaO65%, SiO 2 20%, Al 2 o 3 5%, Fe 2 o 3 2.5%, after the mixture is ground to 120 mesh, it is calcined at 1320°C-1440°C to obtain cement clinker. The resulting mixed gas of sulfur dioxide and sulfur trioxide is dried with concentrated sulfuric acid, mixed with air and compressed, and then passed into the mixed slurry composed of pyrolusite and rhodochrosite. The mixed slurry of pyrolusite and rhodochrosite is prepared as follows: grind the mixed raw materials of pyrolusite and rhodochrosite to 100 mesh, then add water and stir to form a slurry with a solid-to-liquid ratio of 4:1. The quality of pyrolusite in the mixed slurry is its The mass of rhodochrosite is 92% of the theoretical reaction amount of sulfur dioxide in the gas mixture, and 95% of the theoret...
Embodiment 2
[0014] Mix vanadic acid leaching residue from stone coal extraction with lead-zinc tailings in a ratio of 4:1, and add a small amount of bauxite and iron powder, so that the mass percentage of various oxides in the mixture except sulfur is: CaO64.5 %, SiO 2 20.5%, Al 2 o 3 4.5%, Fe 2 o 3 2%, after the mixture is ground to 120 mesh, it is calcined at 1330°C-1450°C to obtain cement clinker. The mixed gas of sulfur dioxide and sulfur trioxide produced by calcination is dried with concentrated sulfuric acid, mixed with air and compressed, and then passed into the mixed slurry of pyrolusite and rhodochrosite. The mixed slurry of pyrolusite and rhodochrosite is prepared as follows: grind the mixed raw materials of pyrolusite and rhodochrosite to 100 mesh, add water and stir to form a slurry with a solid-to-liquid ratio of 5:1, and the quality of pyrolusite in the mixed slurry is equal to that of the mixed gas The mass of rhodochrosite is 92% of the theoretical reaction amoun...
Embodiment 3
[0016] Mix acid leaching electrolytic manganese slag and limestone in a ratio of 4.5:1, and add a small amount of diaspore and iron powder, so that the mass percentages of various oxides in the mixture are: CaO65%, SiO 2 20%, Al 2 o 3 5%, Fe 2 o 3 2.5%, after grinding the mixture to 120 mesh, calcining at 1360°C-1460°C to obtain cement clinker. The mixed gas of sulfur dioxide and sulfur trioxide produced by calcination is dried with concentrated sulfuric acid, mixed with air and compressed, and then passed into the mixed slurry of pyrolusite and rhodochrosite. The mixed slurry of pyrolusite and rhodochrosite is prepared as follows: grind the mixed raw materials of pyrolusite and rhodochrosite to 100 mesh, add water and stir to form a slurry with a solid-to-liquid ratio of 4:1, and the quality of pyrolusite in the mixed slurry is equal to that in the mixed gas. The theoretical reaction amount of sulfur dioxide is 92%, and the mass of rhodochrosite is 95% of the theoretic...
PUM
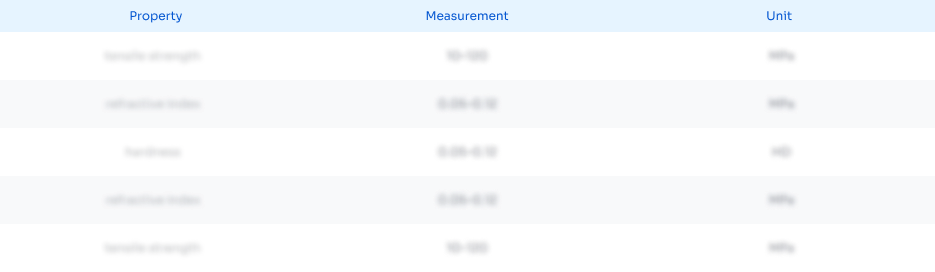
Abstract
Description
Claims
Application Information

- Generate Ideas
- Intellectual Property
- Life Sciences
- Materials
- Tech Scout
- Unparalleled Data Quality
- Higher Quality Content
- 60% Fewer Hallucinations
Browse by: Latest US Patents, China's latest patents, Technical Efficacy Thesaurus, Application Domain, Technology Topic, Popular Technical Reports.
© 2025 PatSnap. All rights reserved.Legal|Privacy policy|Modern Slavery Act Transparency Statement|Sitemap|About US| Contact US: help@patsnap.com