Shape dyeing process for cotton/fibers
A fiber and form technology, applied in the field of cotton/fiber form dyeing process, can solve the problems of repeated labor sewage discharge, increase dyeing cost, long process flow, etc., to reduce sewage discharge treatment and environmental pollution, reduce repeated investment, simplify The effect of the process flow
- Summary
- Abstract
- Description
- Claims
- Application Information
AI Technical Summary
Problems solved by technology
Method used
Examples
Embodiment 1
[0014] Step 1: Place bobbins and warp beams on the same yarn carrier, add refining agent, caustic soda, and hydrogen peroxide at a rate of 3g of refining agent, 3g of caustic soda, and 5g of hydrogen peroxide per liter of water at room temperature, and mix evenly to make a mixing aid , then put the bobbin and warp beam into the mixing aid with a bath ratio of 1:10, heat up to 100°C at 2°C / min, keep for 60 minutes, and get rid of the mixing aid.
[0015] Step 2: Dyeing at a constant temperature of 60°C, inject clean water at room temperature, add dyes into the clear water, then raise the temperature to 60°C, add sodium starch powder and keep it for 30 minutes, add soda ash for 60 minutes, and drain the waste water.
[0016] Step 3: Wash with water at 60°C, add glacial acetic acid with a mass concentration of 85% at a ratio of 0.5g / l, drain the waste liquid after 15 minutes, then inject water, add soaping agent at a ratio of 2g / l, and soap at 90°C 115 minutes, remove the waste l...
Embodiment 2
[0019] Step 1: Place bobbins and warp beams on the same yarn carrier, add refining agent, caustic soda, and hydrogen peroxide at a rate of 3g of refining agent, 3g of caustic soda, and 5g of hydrogen peroxide per liter of water at room temperature, and mix evenly to make a mixing aid , then the bobbin and the warp beam are put into the mixing aid with a bath ratio of 1:15, and the temperature is raised to 110° C. at 2° C. / min, and kept for 30 minutes to get rid of the mixing aid.
[0020] Step 2: Dyeing at a constant temperature of 60°C, inject clean water at room temperature, add dyes into the clear water, then raise the temperature to 60°C, add sodium starch powder and keep for 30 minutes, add soda ash for 60 minutes, and drain waste water.
[0021] Step 3: wash with water at 60°C, add glacial acetic acid with a mass concentration of 85% at a ratio of 1g / l, drain the waste liquid after 15 minutes, then inject water, add soaping agent at a ratio of 2g / l, and soap at 95°C for 1...
PUM
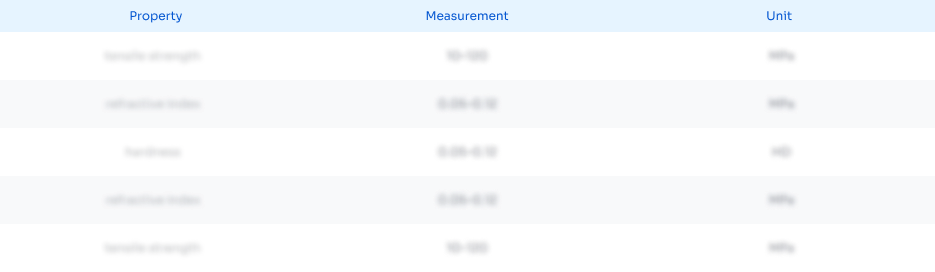
Abstract
Description
Claims
Application Information

- Generate Ideas
- Intellectual Property
- Life Sciences
- Materials
- Tech Scout
- Unparalleled Data Quality
- Higher Quality Content
- 60% Fewer Hallucinations
Browse by: Latest US Patents, China's latest patents, Technical Efficacy Thesaurus, Application Domain, Technology Topic, Popular Technical Reports.
© 2025 PatSnap. All rights reserved.Legal|Privacy policy|Modern Slavery Act Transparency Statement|Sitemap|About US| Contact US: help@patsnap.com