After-finishing process of linen fabric
A linen fabric and finishing technology, applied in fiber processing, plant fibers, textiles and papermaking, etc., can solve the problems of poor wearing shape and easy wrinkling of linen fabrics, and achieve the improvement of easy wrinkling, long-lasting finishing effect and stable color. Effect
- Summary
- Abstract
- Description
- Claims
- Application Information
AI Technical Summary
Problems solved by technology
Method used
Examples
Embodiment 1
[0022] A kind of technology of linen fabric post-finishing, the finishing liquid used is the finishing liquid of chitosan degraded by citric acylation.
[0023] (1) Carry out finishing solution padding to the linen fabric of scouring and bleaching, use citricylated degraded chitosan finishing solution, its composition and weight ratio are: citricylated degraded chitosan consumption 4%, catalyst The dosage of sodium hypophosphite is 4%; the finishing bath uses water as a solvent, and the above-mentioned finishing solution is added, and the ratio of finishing solution to water is 1:20, and a softener and a penetrating agent are also added in the finishing bath. Softening agent and penetration agent here are prior art.
[0024] (2) Pre-baking the fabric, the pre-baking temperature is 80°C, and the pre-baking time is 150 seconds; (3) The fabric is baked at a high temperature, the baking temperature is 160°C, and the baking time is 180 seconds.
Embodiment 2
[0026] A kind of technology of linen fabric post-finishing, the finishing liquid used is the finishing liquid of chitosan degraded by citric acylation.
[0027] (1) Use the citricylated degraded chitosan finishing solution, its composition and weight ratio are: citricylated degraded chitosan consumption 5%, catalyst sodium hypophosphite 3%; the rest is the same as Example 1.
[0028] (2) Pre-baking the fabric, the pre-baking temperature is 85°C, and the pre-baking time is 120 seconds; (3) Carrying out high-temperature baking to the fabric, the baking temperature is 180°C, and the baking time is 150 seconds.
Embodiment 3
[0030] A finishing process for linen fabrics, the finishing solution used is a compound finishing solution of citric acid degraded chitosan and citric acid.
[0031] (1) Carry out finishing liquid padding treatment to the flax fabric that has been scoured and bleached, and the finishing liquid is a compound finishing liquid of citric acid degraded chitosan and citric acid, and its composition and weight ratio are: finishing agent citric acid The dosage of degrading chitosan is 3%, the dosage of citric acid is 1%, and the dosage of catalyst sodium hypophosphite is 4%.
[0032] (2) Pre-baking the fabric, the pre-baking temperature is 75°C, and the pre-baking time is 120 seconds; (3) Carrying out high-temperature baking to the fabric, the baking temperature is 155°C, and the baking time is 120 seconds.
PUM
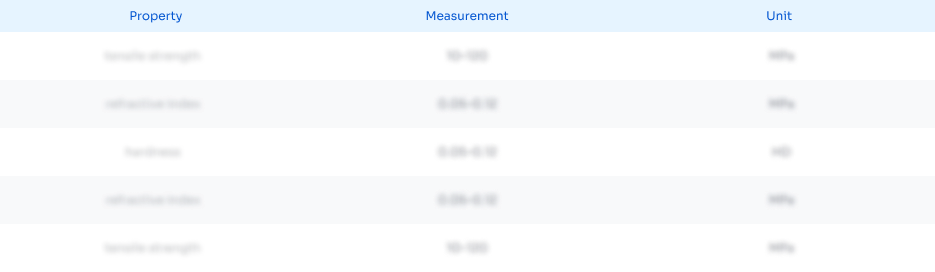
Abstract
Description
Claims
Application Information

- R&D Engineer
- R&D Manager
- IP Professional
- Industry Leading Data Capabilities
- Powerful AI technology
- Patent DNA Extraction
Browse by: Latest US Patents, China's latest patents, Technical Efficacy Thesaurus, Application Domain, Technology Topic, Popular Technical Reports.
© 2024 PatSnap. All rights reserved.Legal|Privacy policy|Modern Slavery Act Transparency Statement|Sitemap|About US| Contact US: help@patsnap.com