Novel process for efficiently and continuously synthesizing 2-naphthol
A high-efficiency, new process technology, applied in the field of organic chemical synthesis, can solve the problems of intermittent synthesis process, poor working conditions, high synthesis cost, etc., and achieve the effect of improved synthesis efficiency, stable performance, and reduced discharge of three wastes
- Summary
- Abstract
- Description
- Claims
- Application Information
AI Technical Summary
Problems solved by technology
Method used
Image
Examples
Embodiment 1
[0027] Naphthalene is sulfonated with 96% sulfuric acid at 155-165°C to mainly obtain 2-naphthalenesulfonic acid (content 85%), 1-naphthalenesulfonic acid (content 10%), add sodium sulfite (by-product during alkali fusion) It was precipitated, heated and concentrated to obtain 2-naphthalenesulfonic acid sodium salt. Then carry out alkaline melting of 2-naphthalenesulfonate sodium in a stirred cast iron or zinc steel kettle. First add 50% sodium hydroxide solution, heat to 300°C, add 2-naphthalenesulfonate sodium after dehydration, and keep at 320°C for about 3h. After the melt is dissolved in water, sulfur dioxide is added for acidification, neutralized to weakly alkaline (pH=8), after phase separation, the organic phase is crude naphthol, and the aqueous phase is mixed with tributyl phosphate, toluene 1:1 (v / v) mixed solvent to extract naphthol, and rectify together with the organic phase, reclaim the solvent, and obtain 2-naphthol and 1-naphthol. The purity of 2-naphthol ...
Embodiment 2
[0029] Naphthalene is sulfonated with 96% sulfuric acid at 140-155°C to mainly obtain 2-naphthalenesulfonic acid (content 85%), 1-naphthalenesulfonic acid (content 10%), adding sodium sulfite (by-product during alkali fusion) to make After precipitation, heating and concentration, 2-naphthalenesulfonic acid sodium salt was obtained. Then dissolve the sodium 2-naphthalenesulfonate in a stirred cast iron or zinc steel kettle. First add 50% sodium carbonate solution, heat to 250°C, add 2-sodium naphthalenesulfonate after dehydration, and keep at 300°C for about 3h. After the melt is dissolved in water, dilute sulfuric acid is added for acidification, neutralized to weakly alkaline (pH=8), after phase separation, the organic phase is crude naphthol, and the aqueous phase is extracted with a trioctylamine solvent to increase the concentration of naphthol. The yield is rectified together with the organic phase, and the solvent is recovered to obtain 2-naphthol and 1-naphthol. The ...
Embodiment 3
[0031] Naphthalene is sulfonated with 96% sulfuric acid at 160-170°C to mainly obtain 2-naphthalenesulfonic acid (content 85%) and 1-naphthalenesulfonic acid (content 10%), which are precipitated by adding sodium hydroxide solution, heated and concentrated Finally, the sodium salt of 2-naphthalenesulfonic acid was obtained. Then dissolve the sodium 2-naphthalenesulfonate in a stirred cast iron or zinc steel kettle. First add 50% sodium sulfite solution, heat to 300°C, add 2-naphthalenesulfonate sodium after dehydration, and keep at 350°C for about 3h. After the melt is dissolved in water, dilute sulfuric acid is added for acidification, neutralized to weakly alkaline (pH=8), after phase separation, the organic phase is crude naphthol, and the aqueous phase is mixed with tributyl phosphate, toluene 1:1 (v / v) mixed solvent to extract, to improve the yield of naphthol, together with the rectification of the organic phase, reclaim the solvent to obtain 2-naphthol and 1-naphthol....
PUM
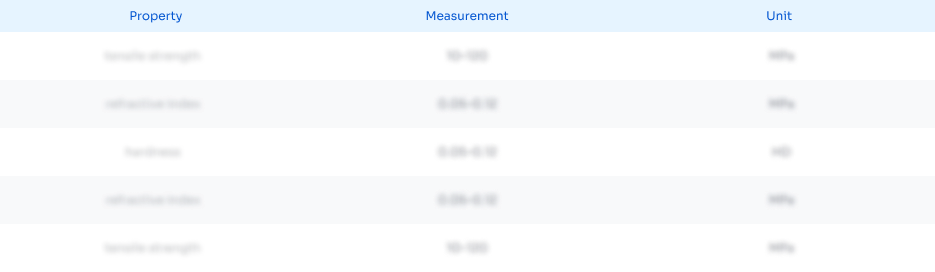
Abstract
Description
Claims
Application Information

- R&D
- Intellectual Property
- Life Sciences
- Materials
- Tech Scout
- Unparalleled Data Quality
- Higher Quality Content
- 60% Fewer Hallucinations
Browse by: Latest US Patents, China's latest patents, Technical Efficacy Thesaurus, Application Domain, Technology Topic, Popular Technical Reports.
© 2025 PatSnap. All rights reserved.Legal|Privacy policy|Modern Slavery Act Transparency Statement|Sitemap|About US| Contact US: help@patsnap.com