Excavator swing arm descending hydraulic control loop
A technology of control circuit and mobile arm, which is applied in the direction of earth mover/shovel, construction, etc., can solve the problems of increased displacement, negative pressure of the arm, and lack of reception, so as to prevent the phenomenon of suction and reduce the system Effect of oil temperature and power consumption reduction
- Summary
- Abstract
- Description
- Claims
- Application Information
AI Technical Summary
Problems solved by technology
Method used
Image
Examples
Embodiment Construction
[0013] As shown in the drawings, a hydraulic control circuit for excavator boom lowering includes a variable displacement hydraulic pump 7 controlled by a servo variable mechanism connected through pipelines, a boom bidirectional hydraulic control reversing valve 3 and a boom cylinder 2 .
[0014] The servo variable mechanism is a well-known mechanism, and its usual structure is to set a servo piston in the housing, and the servo piston is connected to a swash plate through a hinge, and the swash plate swing angle can be changed when the hydraulic oil pushes the piston to move. size, thereby changing the displacement of the variable displacement hydraulic pump 7.
[0015] The boom two-way hydraulic control reversing valve 3 is preferably a three-position six-way two-way hydraulic control reversing valve with regeneration function (for the so-called "regeneration", refer to the second paragraph of the background technology part), the three-position six-way two-way hydraulic con...
PUM
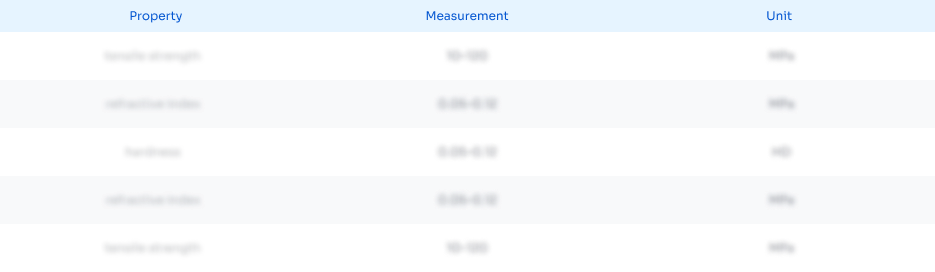
Abstract
Description
Claims
Application Information

- Generate Ideas
- Intellectual Property
- Life Sciences
- Materials
- Tech Scout
- Unparalleled Data Quality
- Higher Quality Content
- 60% Fewer Hallucinations
Browse by: Latest US Patents, China's latest patents, Technical Efficacy Thesaurus, Application Domain, Technology Topic, Popular Technical Reports.
© 2025 PatSnap. All rights reserved.Legal|Privacy policy|Modern Slavery Act Transparency Statement|Sitemap|About US| Contact US: help@patsnap.com