Anti-static flame-retardant plastic for roller of underground conveying belt of coal mine
A technology of flame-retardant plastics and conveyor belts, which is applied in the direction of conveyor objects, rollers, transportation and packaging, etc. It can solve the problems of reduced material strength, impact toughness, low thermal deformation temperature, and high water absorption, and achieve good flame-retardant effects Effect
- Summary
- Abstract
- Description
- Claims
- Application Information
AI Technical Summary
Problems solved by technology
Method used
Examples
Embodiment 1
[0042] Take raw material PA66 slice 45g (viscosity is 2.4), glass fiber 35g, POE graft 7g, red phosphorus flame retardant 11g, ethoxylated alkylamine 0.7g, antioxidant is 1098 is 0.7g, calcium stearate 0.6g, except for glass fiber, put other raw materials into the high mixer and mix for 3 minutes, then add the mixed raw materials into glass fiber and put them in the twin-screw extruder, the screw speed is 250 rpm, and the processing temperature is 290 ℃, extrusion granulation.
Embodiment 2
[0044] Take raw material PA66 slice 45g (viscosity is 2.8), glass fiber 30g, POE graft 11g, red phosphorus flame retardant 12g, ethoxylated alkylamine 0.7g, antioxidant 168 is 0.7g, calcium stearate 0.6g, except for glass fiber, put other raw materials into the high mixer and mix for 2.5 minutes, then add the mixed raw materials into glass fiber and put them in the twin-screw extruder, the screw speed is 260 rpm, and the processing temperature is 270 ℃, extrusion granulation.
Embodiment 3
[0046] Take raw material PA66 slice 40g (viscosity is 3.0), glass fiber 35g, POE graft 18g, red phosphorus flame retardant 5g, ethoxylated alkylamine 0.9g, antioxidant is 1010 is 0.6g, calcium stearate 0.5g, except for glass fiber, put other raw materials into a high mixer and mix for 3 minutes, then add the mixed raw materials into glass fiber and put them in a twin-screw extruder, the screw speed is 350 rpm, and the processing temperature is 280 ℃, extrusion granulation.
PUM
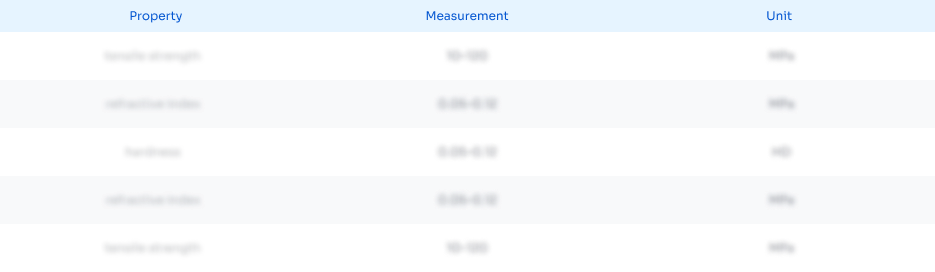
Abstract
Description
Claims
Application Information

- Generate Ideas
- Intellectual Property
- Life Sciences
- Materials
- Tech Scout
- Unparalleled Data Quality
- Higher Quality Content
- 60% Fewer Hallucinations
Browse by: Latest US Patents, China's latest patents, Technical Efficacy Thesaurus, Application Domain, Technology Topic, Popular Technical Reports.
© 2025 PatSnap. All rights reserved.Legal|Privacy policy|Modern Slavery Act Transparency Statement|Sitemap|About US| Contact US: help@patsnap.com