Ozonolysis catalyst and preparation method thereof
A technology of ozone decomposition and catalyst, applied in separation methods, chemical instruments and methods, physical/chemical process catalysts, etc., can solve the problems of complex equipment structure, difficulty in widespread promotion, high production cost, etc., and achieve simple preparation process and convenient use , low cost effect
- Summary
- Abstract
- Description
- Claims
- Application Information
AI Technical Summary
Problems solved by technology
Method used
Image
Examples
preparation example Construction
[0026] Correspondingly provide the preparation method of above-mentioned ozonolysis catalyst, see below figure 2 Shown ozonolysis catalyst preparation flowchart, this preparation method is described in detail, comprises the following steps:
[0027] Step 210, preparing active ingredient solution:
[0028] Ferric nitrate--Fe(NO 3 ) 3 As an active component, Fe(NO 3 ) 3 solution; or manganese nitrate--Mn(NO 3 ) 2 As an active component, Mn(NO 3 ) 2 solution.
[0029] Step 220, cleaning and drying the nickel foam as the carrier:
[0030] The nickel foam that will contain irregular pores, for example, adopts 70 mesh, 80 mesh, 100 mesh or 120 mesh (the mesh number adopts the American standard, and the selected mesh number takes into account the two factors of large catalyst carrying capacity and small wind resistance) The nickel foam was washed with 0.1M KOH and 0.1M HCl respectively (M is the molar concentration, ie mol / L), rinsed with distilled water, and dried at 120°...
Embodiment 1
[0038] The preparation mass fraction is 5% Fe(NO 3 ) 3 Active ingredient solution. Immerse the cleaned and dried nickel foam into the active component solution for 10 to 30 minutes, take it out and dry it in an oven at 80°C to 100°C. The dried catalyst carrier was baked at 300° C. for 2 hours, and cooled naturally in the furnace. Repeat the impregnation, drying, and baking operations 1 to 2 times to adjust the loading amount of the catalyst active component. The mass percentage of iron oxide in the prepared ozonolysis catalyst is about 1-2%.
Embodiment 2
[0040] The preparation mass fraction is 10% Fe(NO 3 ) 3 solution. Immerse the cleaned foamed nickel into the active component solution for 10 to 30 minutes, take it out and dry it in an oven at 80°C to 100°C. The dried catalyst carrier was baked at 300° C. for 2 hours, and cooled naturally in the furnace. Repeat the impregnation, drying, and baking operations 1 to 2 times to adjust the loading amount of the catalyst active component. The mass percentage of iron oxide in the prepared ozonolysis catalyst is about 2-5%.
PUM
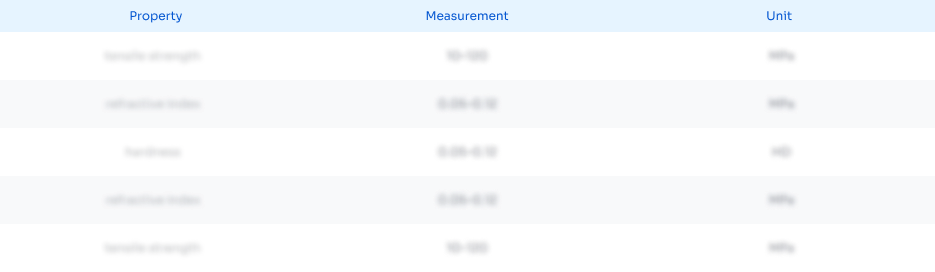
Abstract
Description
Claims
Application Information

- R&D
- Intellectual Property
- Life Sciences
- Materials
- Tech Scout
- Unparalleled Data Quality
- Higher Quality Content
- 60% Fewer Hallucinations
Browse by: Latest US Patents, China's latest patents, Technical Efficacy Thesaurus, Application Domain, Technology Topic, Popular Technical Reports.
© 2025 PatSnap. All rights reserved.Legal|Privacy policy|Modern Slavery Act Transparency Statement|Sitemap|About US| Contact US: help@patsnap.com