Method for manufacturing steel ball for fan bearing
A technology of bearing steel and manufacturing method, applied in the field of steel ball manufacturing, can solve the problems of low bearing capacity, short service life, small bearing load, etc., and achieve the effect of tight internal organization
- Summary
- Abstract
- Description
- Claims
- Application Information
AI Technical Summary
Problems solved by technology
Method used
Image
Examples
Embodiment 1
[0019] Steel balls for fan bearings, The manufacturing method includes a grinding step, wherein a hot heading process and a continuous annealing process are arranged before the grinding step.
[0020] In this embodiment, the hot heading process includes blanking-finishing-heating-forming-cooling. The hot upsetting process adopts upsetting extrusion, and its metallographic structure is fine and compact, and the metal wire flow is in two arc shapes (arch type), which is resistant to pressure and impact.
[0021] The rolling system adopts rolling extrusion. Although the metallographic structure is affected by external forces, the change is small, the wire flow is irregular, and there are many divergence points. The pressure resistance and impact resistance are worse than thermal upsetting.
[0022] The heating temperature of the hot heading process is 800°C, and the heating time is 0.5 hours. The cooling of the hot heading process adopts direct air cooling.
[0023] In this e...
Embodiment 2
[0028] In this embodiment, the steel balls for fan bearings, The manufacturing method includes a grinding step, wherein a hot heading process and a continuous annealing process are arranged before the grinding step. The heating temperature of the hot heading process is 850°C, and the heating time is 1 hour. The preheating temperature of the continuous annealing process is 450° C., and the preheating time is 1 hour. The heating temperature of the continuous annealing process is 700° C., and the heating time is 1 hour. The constant temperature of the continuous annealing process is 780° C., and the constant temperature time is 4 hours. The air cooling temperature for the continuous annealing process is 600°C.
[0029] In the grinding step, a lapping plate is used as the grinding plate, and chromium trioxide is used as the abrasive for grinding. The water solvent for the lapping plate is a mixed water agent with the characteristics and functions of lubricating, cooling, clean...
Embodiment 3
[0033] In this embodiment, the steel balls for fan bearings, The manufacturing method includes a grinding step, wherein a hot heading process and a continuous annealing process are arranged before the grinding step. The heating temperature of the hot heading process is 825°C, and the heating time is 0.75 hours. The preheating temperature of the continuous annealing process is 450° C., and the preheating time is 1 hour. The heating temperature of the continuous annealing process is 700° C., and the heating time is 1 hour. The constant temperature of the continuous annealing process is 790° C., and the constant temperature time is 4.5 hours. The air-cooling temperature for the continuous annealing process is 600°C.
[0034] In the grinding step, a lapping plate is used as the grinding plate, and chromium trioxide is used as the abrasive for grinding. The water solvent for the lapping plate is a mixed water agent with the characteristics and functions of lubricating, cooling,...
PUM
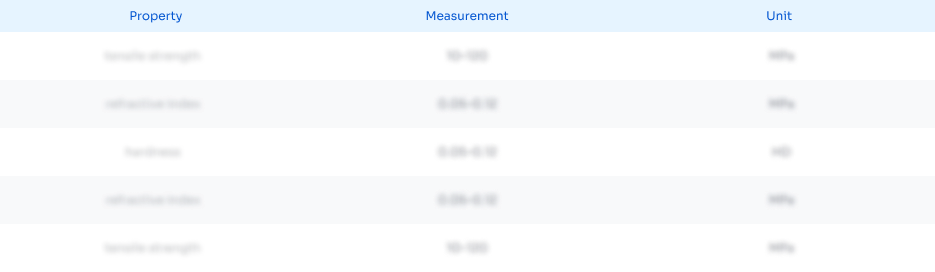
Abstract
Description
Claims
Application Information

- R&D
- Intellectual Property
- Life Sciences
- Materials
- Tech Scout
- Unparalleled Data Quality
- Higher Quality Content
- 60% Fewer Hallucinations
Browse by: Latest US Patents, China's latest patents, Technical Efficacy Thesaurus, Application Domain, Technology Topic, Popular Technical Reports.
© 2025 PatSnap. All rights reserved.Legal|Privacy policy|Modern Slavery Act Transparency Statement|Sitemap|About US| Contact US: help@patsnap.com