Method to toughen and malleableize the amorphous alloy by ultrasonic processing
An amorphous alloy and ultrasonic treatment technology, which is used in the field of improving the properties of bulk amorphous alloys, can solve problems such as failure, and achieve the effects of excellent fracture strength, simple equipment and process, and improvement of room temperature plastic deformation capacity.
- Summary
- Abstract
- Description
- Claims
- Application Information
AI Technical Summary
Problems solved by technology
Method used
Image
Examples
Embodiment 1
[0025] High energy ultrasonic treatment composition is Zr 55 Al 10 Ni 5 Cu 30 The amorphous alloy, concrete steps are as follows:
[0026] (A) contact the horn of the ultrasonic oscillator with the bottom of the cooling water tank;
[0027] (B) Zr 55 Al 10 Ni 5 Cu 30 The bulk amorphous alloy is placed in the cooling water tank, and the temperature of the cooling water is adjusted to maintain at 27°C;
[0028] (C) the step of adjusting the output power of the ultrasonic oscillator and the oscillation time; the output power of the ultrasonic oscillator is that the power per unit area is 3 × 10 4 W / mm 2 and remain stable; the ultrasonic oscillation time is 60 hours.
[0029] Test equipment: pressure testing machine
[0030] The Zr after processing according to embodiment 1 method 55 Al 10 Ni 5 Cu 30 The results of the compression test of the bulk amorphous alloy prove that its compressive plasticity is increased from less than 2% to 10% at a temperature of 25°C, an...
Embodiment 2
[0033] High energy ultrasonic treatment composition is Zr 61.88 Al 10 Ni 10.12 Cu 18 The amorphous alloy, concrete steps are as follows:
[0034] Contact the horn of the ultrasonic oscillator with the bottom of the cooling water tank;
[0035] Will Zr 61.88 Al 10 Ni 10.12 Cu 18 The bulk amorphous alloy is placed in the cooling water tank, and the temperature of the cooling water is adjusted to maintain at 30°C;
[0036] Adjust the output power and oscillation time of the ultrasonic oscillator; the output power of the ultrasonic oscillator is 2.7×10 per unit area 4 W / mm 2 and remain stable; the ultrasonic oscillation time is 48 hours.
[0037] According to the Zr after the method of embodiment 2 is processed 61.88 Al 10 Ni 10.12 Gu 18 The results of the compression test of the bulk amorphous alloy prove that its compressive plasticity at a temperature of 25 ° C increases from less than 4.5% to 6.5%, and the increase rate is 44.4%, see Figure 4 shown.
[0038] D...
Embodiment 3
[0040] High energy ultrasonic treatment composition is Zr 65 Al 7.5 Ni 10 Cu 17.5 The amorphous alloy, concrete steps are as follows:
[0041] Contact the horn of the ultrasonic oscillator with the bottom of the cooling water tank;
[0042] Will Zr 65 Al 7.5 Ni 10 Cu 17.5 The bulk amorphous alloy is placed in the cooling water tank, and the temperature of the cooling water is adjusted to maintain at 25°C;
[0043] Adjust the output power and oscillation time of the ultrasonic oscillator; the output power of the ultrasonic oscillator is that the power per unit area is 3 × 10 4 W / mm 2 and remain stable; the ultrasonic oscillation time is 55 hours.
[0044] According to the Zr after the method of embodiment 3 is processed 65 Al 7.5 Ni 10 Cu 17.5 The results of the compression test of the bulk amorphous alloy prove that its compression plasticity at a temperature of 25°C increases from less than 2.5% to 9%, and the increase rate is 300%, see Figure 5 shown.
[0045]...
PUM
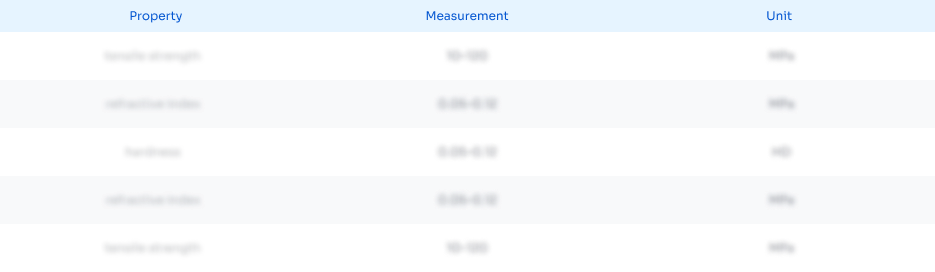
Abstract
Description
Claims
Application Information

- R&D
- Intellectual Property
- Life Sciences
- Materials
- Tech Scout
- Unparalleled Data Quality
- Higher Quality Content
- 60% Fewer Hallucinations
Browse by: Latest US Patents, China's latest patents, Technical Efficacy Thesaurus, Application Domain, Technology Topic, Popular Technical Reports.
© 2025 PatSnap. All rights reserved.Legal|Privacy policy|Modern Slavery Act Transparency Statement|Sitemap|About US| Contact US: help@patsnap.com