Sulphuric acid dew point corrosion resisting steel and method for producing same
A dew point corrosion and sulfuric acid resistance technology, applied in metal rolling, electric furnace, furnace, etc., can solve the problems of no successful experience, high cost, low cost, etc.
- Summary
- Abstract
- Description
- Claims
- Application Information
AI Technical Summary
Problems solved by technology
Method used
Image
Examples
Embodiment 1
[0038] The preparation method of sulfuric acid dew point corrosion-resistant steel described in this implementation, its technological process: electric furnace with refining furnace smelting, refining, thin slab continuous casting, continuous casting slab soaking, high-pressure water descaling, controlled rolling, controlled cooling, coiling Pick.
[0039] Among them, the main chemical composition of molten steel after refining is mass percentage (wt%): C: 0.030%, Si: 0.25%, Mn: 1.0%, P: 0.005%, S: 0.004%, Cu: 0.15%, Cr: 1.0 %, Ni: 0.04%, Sb: 0.15%, Ti: 0.010%, N: 10PPm, and the rest is composed of Fe and unavoidable impurities.
[0040] Thin slab continuous casting and rolling process parameters are: continuous casting at a pulling speed of 3.5m / min, casting slab entering furnace temperature at 900°C, soaking temperature at 1100°C, start rolling temperature at 1040°C, finish rolling temperature at 850°C, The coiling temperature was 550°C.
Embodiment 2
[0042] The preparation method of sulfuric acid dew point corrosion-resistant steel described in this implementation, its technological process: electric furnace with refining furnace smelting, refining, thin slab continuous casting, continuous casting slab soaking, high-pressure water descaling, controlled rolling, controlled cooling, coiling Pick.
[0043] Among them, the main chemical composition of molten steel after refining is mass percentage (wt%): C: 0.040%, Si: 0.15%, Mn: 0.45%, P: 0.008%, S: 0.004%, Cu: 0.20%, Cr: 0.45 %, Sb: 0.040%, Ni: 0.08%, Ti: 0.020%, N: 30PPm, Ni / Cu: 0.4, and the rest is composed of Fe and unavoidable impurities.
[0044] Thin slab continuous casting and rolling process parameters are: continuous casting at a pulling speed of 3.8m / min, slab entering furnace temperature is 920°C, soaking temperature is 1120°C, start rolling temperature is 1060°C, finish rolling temperature is 860°C, The coiling temperature was 560°C.
Embodiment 3
[0046] The preparation method of sulfuric acid dew point corrosion-resistant steel described in this implementation, its technological process: electric furnace with refining furnace smelting, refining, thin slab continuous casting, continuous casting slab soaking, high-pressure water descaling, controlled rolling, controlled cooling, coiling Pick.
[0047] Among them, the main chemical composition of molten steel after refining is mass percentage (wt%): C: 0.055%, Si: 0.25%, Mn: 0.65%, P: 0.015%, S: 0.012%, Cu: 0.25%, Cr: 0.65% %, Sb: 0.075%, Ni: 0.125%, Ti: 0.030%, N: 50PPm, Ni / Cu: 0.5, and the rest is composed of Fe and unavoidable impurities.
[0048] Thin slab continuous casting and rolling process parameters are: continuous casting at a pulling speed of 4.5m / min, casting slab entering furnace temperature at 950°C, soaking temperature at 1150°C, starting rolling temperature at 1080°C, finishing rolling temperature at 900°C, The coiling temperature was 600°C.
PUM
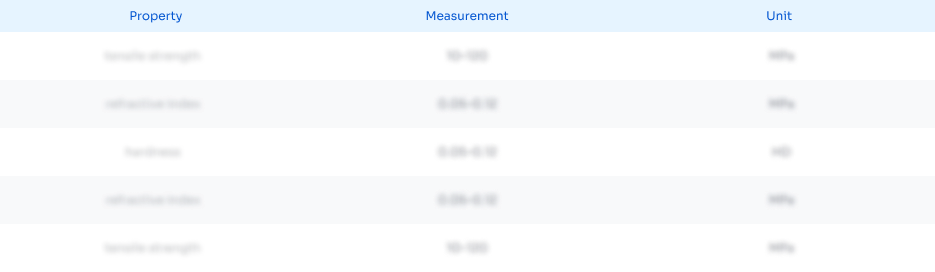
Abstract
Description
Claims
Application Information

- R&D Engineer
- R&D Manager
- IP Professional
- Industry Leading Data Capabilities
- Powerful AI technology
- Patent DNA Extraction
Browse by: Latest US Patents, China's latest patents, Technical Efficacy Thesaurus, Application Domain, Technology Topic, Popular Technical Reports.
© 2024 PatSnap. All rights reserved.Legal|Privacy policy|Modern Slavery Act Transparency Statement|Sitemap|About US| Contact US: help@patsnap.com