Heat accumulating type external heat blast cupola furnace
A regenerative, cupola technology, applied in the field of foundry production, can solve the problems of low heat exchange efficiency of heat exchangers, loss of physical heat of furnace gas, poor adaptability, etc., and achieve the effect of reducing CO2 emissions
- Summary
- Abstract
- Description
- Claims
- Application Information
AI Technical Summary
Problems solved by technology
Method used
Image
Examples
Embodiment Construction
[0014] It can be seen from the schematic diagram of the structure of the regenerative external heat supply cupola shown in the accompanying drawing that the furnace body 4 lined with refractory material welded by steel plates has a taphole 1, and the lower part of the furnace body 4 is equipped with a main wind eye. 2. There is a primary combustion air box 6 in the middle, a furnace gas outlet pipe 7 in the upper part, and a movable and openable furnace cover 31 at the top. The main air box 3 is connected to the main air eye 2, and the primary air eye 5 is connected to the primary air box. 6 is connected, the furnace gas outlet pipe 7 is provided with a thermocouple 8 and a secondary combustion air box 9, the secondary combustion air eye 10 is connected with the secondary combustion air box 9 and the furnace gas outlet pipe 7, and the other end of the furnace gas outlet pipe 7 is connected to the inner The air inlet of the cyclone dust collector 15 lined with refractory insulat...
PUM
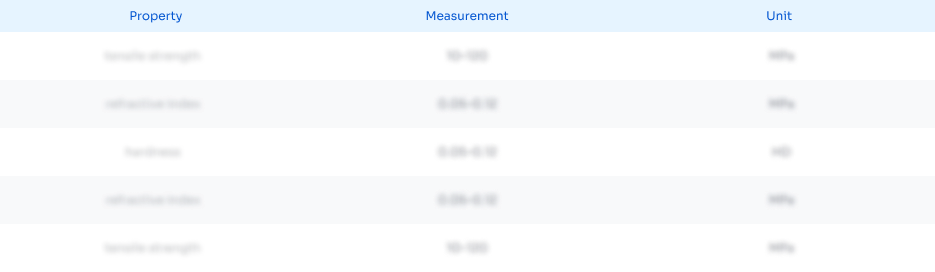
Abstract
Description
Claims
Application Information

- Generate Ideas
- Intellectual Property
- Life Sciences
- Materials
- Tech Scout
- Unparalleled Data Quality
- Higher Quality Content
- 60% Fewer Hallucinations
Browse by: Latest US Patents, China's latest patents, Technical Efficacy Thesaurus, Application Domain, Technology Topic, Popular Technical Reports.
© 2025 PatSnap. All rights reserved.Legal|Privacy policy|Modern Slavery Act Transparency Statement|Sitemap|About US| Contact US: help@patsnap.com