Heatpump type gas-fired boiler waste heat recovery unit
A gas-fired boiler and waste heat recovery technology, applied in the field of energy technology applications, can solve the problems of inability to realize the recovery of flue gas condensation heat, insufficient utilization of sensible heat and latent heat, etc.
- Summary
- Abstract
- Description
- Claims
- Application Information
AI Technical Summary
Problems solved by technology
Method used
Image
Examples
Embodiment 1
[0014] Embodiment 1: see attached figure 1 , in actual operation, natural gas first enters the absorption heat pump unit 1 as a driving heat source, releases heat in its generator, and discharges from the absorption heat pump 1 when the temperature drops to about 130°C, and enters the flue gas together with the exhaust gas of the gas boiler- The water heat exchanger 3 is used as a heating source, and after cooling down to 70°C, it is discharged from the air-water heat exchanger, and the flue gas at 70°C enters the flue gas condensation heat exchanger 2 and is cooled to 30°C before being discharged; the secondary side is 45°C The hot water return water enters the unit in two ways, one way enters the absorption heat pump 1, absorbs heat in its absorber and condenser, and flows out after being heated to about 60°C, and the other way enters the flue gas-water heat exchanger 3, and The flue gas on the primary side undergoes heat exchange, is heated to 60°C and then flows out, and t...
Embodiment 2
[0015] Embodiment 2: see attached figure 2 , Natural gas first enters the absorption heat pump unit 1 as a driving heat source, releases heat in its generator, and is discharged from the absorption heat pump 1 when the temperature drops to about 130°C, and enters the flue gas-water heat exchanger together with the exhaust gas of the gas-fired boiler 3 As a heating source, after cooling down to 70°C, it is discharged from the air-water heat exchanger, and the flue gas at 70°C enters the flue gas condensation heat exchanger 2 and then discharged after cooling down to 30°C; the hot water at 45°C on the secondary side returns to The water enters the absorption heat pump 1, absorbs heat in its absorber and condenser, is heated and then enters the air-water heat exchanger 2, exchanges heat with the primary side flue gas, and is heated to 60°C before being sent to the user.
Embodiment 3
[0016] Embodiment 3: see attached image 3 , in actual operation, natural gas first enters the absorption heat pump unit 1 as the driving heat source, releases heat in its generator, and the flue gas is discharged from the absorption heat pump 1, and enters the flue gas condensation heat exchange together with the 90°C exhaust gas of the gas-fired boiler The heat pump 2 cools down to 30°C and then discharges; the hot water return water at 45°C on the secondary side enters the absorption heat pump 1, is heated to 60°C and then sent to the user.
PUM
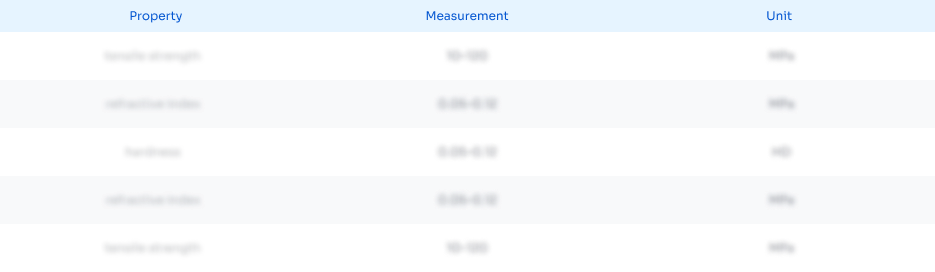
Abstract
Description
Claims
Application Information

- R&D
- Intellectual Property
- Life Sciences
- Materials
- Tech Scout
- Unparalleled Data Quality
- Higher Quality Content
- 60% Fewer Hallucinations
Browse by: Latest US Patents, China's latest patents, Technical Efficacy Thesaurus, Application Domain, Technology Topic, Popular Technical Reports.
© 2025 PatSnap. All rights reserved.Legal|Privacy policy|Modern Slavery Act Transparency Statement|Sitemap|About US| Contact US: help@patsnap.com