Method and equipment for manufacturing bearing ferrule
A bearing ring and manufacturing method technology, applied in the field of bearing parts, can solve the problems of high manufacturing cost, low yield, less than 60%, etc.
- Summary
- Abstract
- Description
- Claims
- Application Information
AI Technical Summary
Problems solved by technology
Method used
Image
Examples
Embodiment Construction
[0022] The present invention as figure 1 , figure 2 As shown, a method for manufacturing a bearing ring includes the following steps:
[0023] (1) Cut the bar material to the specified size and send it in;
[0024] (2) After the heating device makes its temperature reach the predetermined value;
[0025] (3) send into perforating machine to make waste tube, subsequently;
[0026] (4) Cool the waste tube to 640-700°C and transfer it randomly;
[0027] (5) Hot rolling slitting equipment, and through the hot rolling forming and rolling cutting device installed in the hot rolling slitting equipment, the bearing ring blank is processed continuously;
[0028] (6) Shot blasting is carried out on the bearing ring blank and then transferred to the bearing finishing.
[0029] In order to realize the above-mentioned manufacturing method, the present invention provides a kind of equipment for adopting the above-mentioned manufacturing method, including a bar sawing machine, a heatin...
PUM
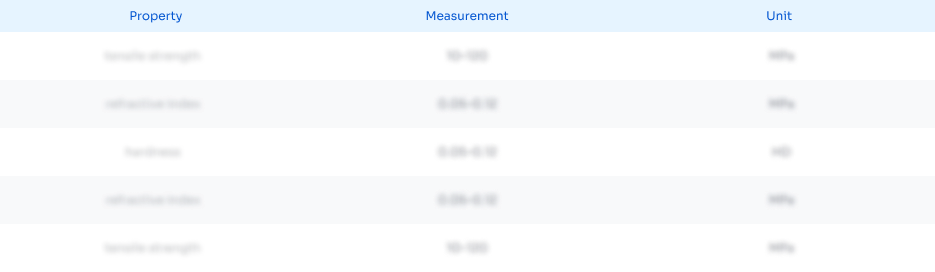
Abstract
Description
Claims
Application Information

- R&D
- Intellectual Property
- Life Sciences
- Materials
- Tech Scout
- Unparalleled Data Quality
- Higher Quality Content
- 60% Fewer Hallucinations
Browse by: Latest US Patents, China's latest patents, Technical Efficacy Thesaurus, Application Domain, Technology Topic, Popular Technical Reports.
© 2025 PatSnap. All rights reserved.Legal|Privacy policy|Modern Slavery Act Transparency Statement|Sitemap|About US| Contact US: help@patsnap.com