Ca-Fe alloy and Al-Ca-Fe alloy for steel making and preparation method thereof
A ferroalloy, aluminum-calcium technology, applied in the field of metallurgical materials, can solve the problems of large calcium burning loss, low calcium content, alloy pulverization, etc., and achieve the effect of reducing calcium burning loss and simple and easy process
- Summary
- Abstract
- Description
- Claims
- Application Information
AI Technical Summary
Problems solved by technology
Method used
Examples
Embodiment 1
[0008] Calcium-iron alloys are melted in a closed induction furnace. The chemical composition of the alloy is Ca 20%, Mg 1%, and the balance is iron and impurities. The capacity of the electric furnace is 500kg. First put 100kg of metal calcium and 5kg of metal magnesium into the furnace, then put in 395kg of scrap steel, and cover the furnace cover. After 10-15 minutes of power transmission, when the temperature in the furnace is around 350°C, inject the flame-retardant mixed gas with an air pump. The mixed gas contains 0.2% (volume) HFC-227ea, and the balance is N 2 , the mixed gas injection is 2L per minute. After about 1 hour, the furnace temperature is 1250°C and the alloy materials in the furnace are all combined and then released from the furnace. Since the protective gas forms a good protective film on the surface of the calcium-iron alloy, no burning of calcium occurs. Its alloy composition: Ca 18.52%, Mg 0.9%, Fe 80.02%, C 0.31%, S 0.02%, P 0.02%. The fire cons...
Embodiment 2
[0012] Melting al-calcium-iron alloy in a closed induction furnace, alloy composition: Ca 10%, Al 40%, the balance is iron and impurities. The capacity of the electric furnace is 500kg. First put 50kg of calcium metal, 200kg of metal aluminum, 5kg of metal magnesium, and 245kg of scrap steel into the furnace, cover the furnace cover, and send electricity for 10-15 minutes. The temperature in the furnace is about 300°C. gas. The flame-retardant mixed gas contains 2% HFC-134ea, and the balance is dry CO 2 mixed protective gas. The flow rate of the mixed gas is 0.9L / min, the temperature in the furnace is about 1200°C in 50 minutes, and the alloy material is melted out of the furnace.
[0013] Its alloy composition: Ca 8.63%, Al 39.81%, Mg 1.10%, Fe 49.08%, C 0.3%, S 0.02%, P 0.02%. The burning loss of Ca is only 1.37% due to the flame-retardant gas protection, and the burning loss of Al is also reduced by 1%. The same method is used to manufacture aluminum-calcium-iron alloys...
Embodiment 3
[0021] Calcium-aluminum alloys are melted in a closed induction furnace.
[0022] Alloy composition: Ca 30%, Al 15%, the balance is Fe and impurities. Electric furnace capacity 500kg. First, 150kg of calcium metal, 75kg of metal aluminum, and 275kg of scrap steel are used, and the process is the same as that of implementation 2. The difference is that the mixed gas contains 5% HFC-227ea, N 2 The balance of 20% is dry compressed air. The mixed gas flow rate is 1.0L per minute.
[0023] Its alloy composition: Ca 28.17%, Al 14.98%, Fe 56.42%, C 0.35%, S0.02%, P 0.02%. The burning loss of Ca is 1.83%.
[0024] Through the above examples, the flame-retardant mixed gas containing HFC-227ea is used for smelting protection of calcium-iron alloy and aluminum-calcium-iron alloy to reduce calcium burning loss, and the process is simple and easy, and the alloy does not pulverize.
PUM
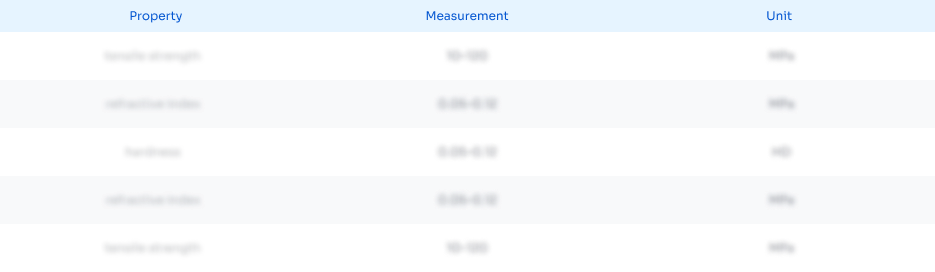
Abstract
Description
Claims
Application Information

- R&D
- Intellectual Property
- Life Sciences
- Materials
- Tech Scout
- Unparalleled Data Quality
- Higher Quality Content
- 60% Fewer Hallucinations
Browse by: Latest US Patents, China's latest patents, Technical Efficacy Thesaurus, Application Domain, Technology Topic, Popular Technical Reports.
© 2025 PatSnap. All rights reserved.Legal|Privacy policy|Modern Slavery Act Transparency Statement|Sitemap|About US| Contact US: help@patsnap.com