Method for preparing contact material having high performance and low mixed copper-chromium alloy content
A copper-chromium alloy and contact material technology, applied in the direction of electrical components, electric switches, circuits, etc., can solve pollution and other problems, and achieve the effect of simple and convenient operation, uniform alloy microstructure, and uniform alloy composition
- Summary
- Abstract
- Description
- Claims
- Application Information
AI Technical Summary
Problems solved by technology
Method used
Examples
Embodiment 1
[0027] Take the copper block and the chromium block each accounting for 50% of the total weight, put them into a vacuum non-consumable arc melting furnace, and evacuate to 8.0×10 -4 After Pa is filled with high-purity argon to 0.6MPa, the power is turned on and the arc is melted into an alloy prefabricated ingot. Push it into the high-frequency induction coil, and evacuate to 7.0×10 -4 After the Pa is filled with high-purity argon to 0.6MPa, the high-frequency power supply is connected, the input current and power are adjusted, the alloy prefabricated ingot is suspended under the action of electromagnetic force, and heated and melted, and the temperature of the alloy ingot is observed by an infrared thermometer After the alloy ingot is completely melted, keep it warm for 10-30 seconds (so that the dissolved gas in the alloy sample can be volatilized as much as possible, reduce the relevant gas content and mix the two evenly), quickly turn off the power, and the sample falls to...
Embodiment 2
[0029] Take the weight ratio of copper block and chromium block as 85:15, vacuumize to 1.5×10 -3 After Pa is filled with high-purity argon to 0.3MPa, induction melting is carried out and cast into alloy prefabricated ingots. The obtained alloy prefabricated ingots are placed in a vacuum electromagnetic levitation melting furnace, and the alloy ingots are pushed into the In the high-frequency induction coil, vacuumize to 1.5×10 -3 After the Pa is filled with high-purity argon to 0.3MPa, the high-frequency power supply is connected, the input current and power are adjusted, the alloy prefabricated ingot is suspended under the action of electromagnetic force, and heated and melted, and the temperature of the alloy ingot is observed by an infrared thermometer , remove the alumina ceramic support rod, after the alloy ingot is completely melted, keep it warm for 10-30 seconds, blow high-purity helium from the hollow alumina ceramic rod, and cool and solidify the sample under high-pu...
Embodiment 3
[0031] Take a copper block and a chromium block with a weight ratio of 70:30, put it into the vacuum induction melting, and evacuate to 1.0×10 - 3 After Pa is filled with high-purity argon to 0.5MPa, induction melting is carried out and cast into an alloy preform, and the obtained alloy preform is put into a cold crucible melting furnace, and the vacuum is evacuated to 1.0×10 -3 After Pa is filled with high-purity argon gas to 0.5MPa, the high-frequency power supply is connected, the input current and power are adjusted, the alloy prefabricated ingot is suspended under the action of electromagnetic force, and heated and melted, and the temperature of the alloy ingot is observed by an infrared thermometer , after the alloy ingot is completely melted, keep it warm for 10-30 seconds, turn off the power quickly, the sample falls into the copper crucible under the action of gravity, cool and solidify rapidly to obtain the alloy ingot.
PUM
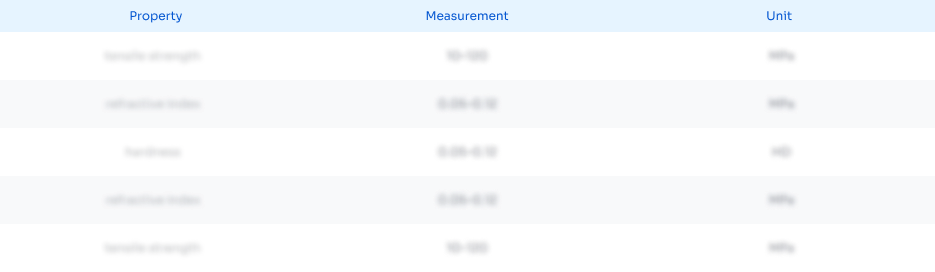
Abstract
Description
Claims
Application Information

- Generate Ideas
- Intellectual Property
- Life Sciences
- Materials
- Tech Scout
- Unparalleled Data Quality
- Higher Quality Content
- 60% Fewer Hallucinations
Browse by: Latest US Patents, China's latest patents, Technical Efficacy Thesaurus, Application Domain, Technology Topic, Popular Technical Reports.
© 2025 PatSnap. All rights reserved.Legal|Privacy policy|Modern Slavery Act Transparency Statement|Sitemap|About US| Contact US: help@patsnap.com