Water lubrication dynamic and static pressure ladder groove step bearing
A stepped bearing, dynamic and static pressure technology, applied in the direction of bearings, bearing components, shafts and bearings, etc., can solve the problems of reducing bearing reliability, instability of the spindle center position, cavitation of lubricating medium, etc.
- Summary
- Abstract
- Description
- Claims
- Application Information
AI Technical Summary
Problems solved by technology
Method used
Image
Examples
Embodiment Construction
[0015] The present invention will be described in further detail below in conjunction with the accompanying drawings.
[0016] Referring to Fig. 1, including the bearing bush 1 and the main shaft 2 arranged in the bearing bush 1, a trapezoidal ring groove 3 is opened on the inner wall of the bearing bush 1, that is, the oil seal surface of the bearing, and the trapezoidal ring groove 3 divides the bearing bush into several In the annular groove 3 of the trapezoidal structure, there is a shallow cavity 4 with a depth smaller than that of the annular groove 3, and on the bearing bush 1, there are oil inlet holes 5 and cooling holes connected to the annular groove 3 of the trapezoidal structure. Hole 6.
[0017] This invention has following three advantages:
[0018] 1. Reduce the temperature rise of the bearing outlet
[0019] The ring groove 3 of the trapezoidal structure divides the axial oil sealing surface 7 with strong dynamic pressure effect into two parts, forming a hyd...
PUM
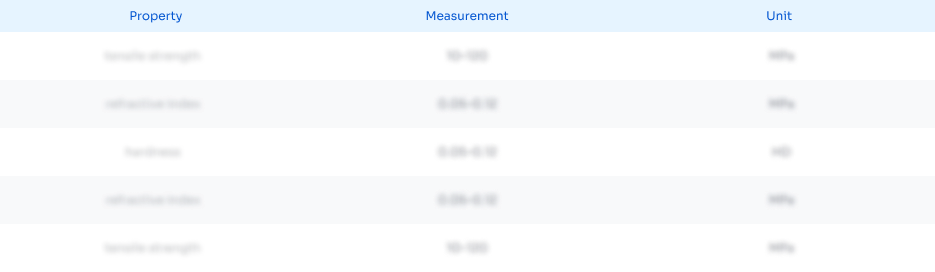
Abstract
Description
Claims
Application Information

- R&D
- Intellectual Property
- Life Sciences
- Materials
- Tech Scout
- Unparalleled Data Quality
- Higher Quality Content
- 60% Fewer Hallucinations
Browse by: Latest US Patents, China's latest patents, Technical Efficacy Thesaurus, Application Domain, Technology Topic, Popular Technical Reports.
© 2025 PatSnap. All rights reserved.Legal|Privacy policy|Modern Slavery Act Transparency Statement|Sitemap|About US| Contact US: help@patsnap.com