Power generation system using waste heat of sintering circular cooler
A technology of sintering ring cooler and waste heat power generation, which is applied in waste heat treatment, machine/engine, steam generation method using heat carrier, etc. It can solve the problems of poor material cooling effect, no obvious increase in power generation, and low main steam parameters. , to achieve the effect of improving efficiency
- Summary
- Abstract
- Description
- Claims
- Application Information
AI Technical Summary
Problems solved by technology
Method used
Image
Examples
Embodiment Construction
[0046] The invention provides a sintering ring cooler exhaust gas waste heat power generation system, which is used for increasing the inlet temperature of waste heat boiler waste gas without affecting the sintering process performance.
[0047] see image 3 , which is a structural diagram of the first embodiment of the exhaust gas waste heat power generation system of the sintered ring cooler according to the present invention.
[0048] In general, the average ore temperature at the inlet 1 of the annular cooler is between 700 and 800°C, and the ore temperature at the outlet 2 of the annular cooler is required to be below 150°C. During the cooling process of the sinter, the heat carried by the sinter is converted into sensible heat of the waste gas, the temperature of the waste gas gradually decreases from front to back, and the temperature of the waste gas at the ore feeding part is the highest. During blast cooling, according to the test, it is generally around 450°C, and ...
PUM
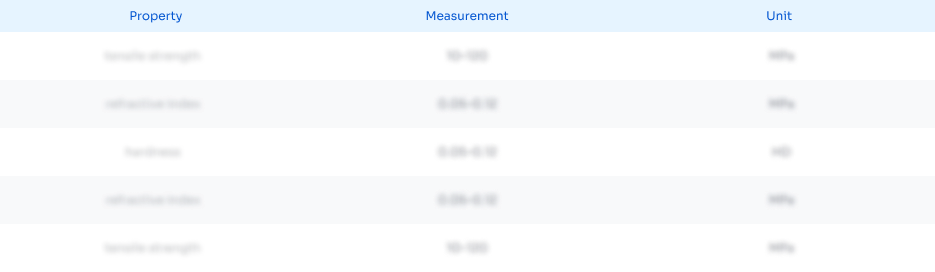
Abstract
Description
Claims
Application Information

- R&D
- Intellectual Property
- Life Sciences
- Materials
- Tech Scout
- Unparalleled Data Quality
- Higher Quality Content
- 60% Fewer Hallucinations
Browse by: Latest US Patents, China's latest patents, Technical Efficacy Thesaurus, Application Domain, Technology Topic, Popular Technical Reports.
© 2025 PatSnap. All rights reserved.Legal|Privacy policy|Modern Slavery Act Transparency Statement|Sitemap|About US| Contact US: help@patsnap.com