Cover glaze and preparation method thereof
A surface glaze and matte technology, applied in the field of ceramic raw materials, can solve the problems of insufficient anti-fouling performance, poor high temperature fluidity, production scheduling restrictions, etc., to achieve smooth, transparent and bright surface, low production cost, and wide firing temperature. Effect
- Summary
- Abstract
- Description
- Claims
- Application Information
AI Technical Summary
Problems solved by technology
Method used
Examples
Embodiment Construction
[0020] The component weight ratio of the surface glaze of the present invention is: 95% of matte frit, 4.3% of air knife soil, 0.1% of sodium carboxymethyl cellulose, 0.35% of industrial sodium tripolyphosphate, 0.25% of ceramic debonding agent, and the above-mentioned 35% water in raw material ratio. Its preparation method steps are; First, prepare required raw materials matt frit, air knife soil, sodium carboxymethyl cellulose, industrial sodium tripolyphosphate, ceramic debonding agent from the market, the matt frit It is a commercially available Jincai frit from Foshan Gaoming Jincai Ceramics Chemical Factory, the size of which is in the shape of rice grains; the above-mentioned incoming raw materials are inspected, and after passing the inspection, the above-mentioned raw materials and water are stirred and mixed evenly at room temperature to form a certain stable colloidal dispersion system, the wet ball milling process is carried out at room temperature, the ball millin...
PUM
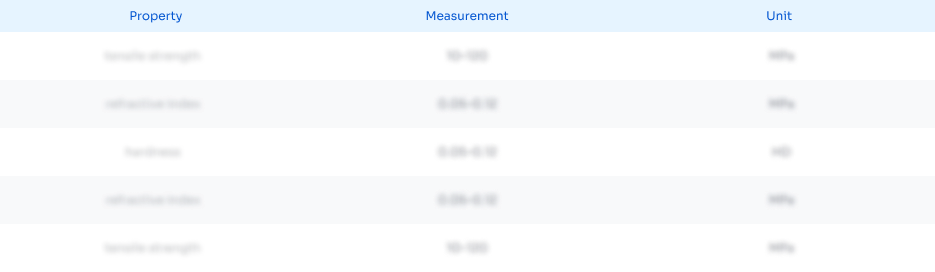
Abstract
Description
Claims
Application Information

- R&D
- Intellectual Property
- Life Sciences
- Materials
- Tech Scout
- Unparalleled Data Quality
- Higher Quality Content
- 60% Fewer Hallucinations
Browse by: Latest US Patents, China's latest patents, Technical Efficacy Thesaurus, Application Domain, Technology Topic, Popular Technical Reports.
© 2025 PatSnap. All rights reserved.Legal|Privacy policy|Modern Slavery Act Transparency Statement|Sitemap|About US| Contact US: help@patsnap.com