Clean production method for preparing sodium chromate from chromite
A technology of sodium chromate and chromite, which is applied in the direction of chromate/dichromate, etc., can solve the problems of equipment corrosion and high reaction temperature, and achieve the effect of reducing the amount of slag discharge
- Summary
- Abstract
- Description
- Claims
- Application Information
AI Technical Summary
Problems solved by technology
Method used
Image
Examples
Embodiment 1
[0023] NaOH-NaNO recycled back to the reactor 3 Medium, after NaOH was added, the temperature was raised to 280°C, chromite was added, oxygen was introduced, and the reaction was carried out under complete mixing conditions for 6 hours, wherein the weight ratio of NaOH to ore was 4:1, and NaNO 3 The weight ratio with ore is 1:1. Finally get NaOH-NaNO 3 The mixed reaction product of medium, chromium salt and iron slag, the conversion rate of chromium is 99%. The mixed reaction product is leached with the iron slag washing solution, the lye is separated from the leaching slurry first, and then the iron slag is separated from the sodium chromate leaching solution; the sodium chromate solution is evaporated and crystallized, and the crystal is rinsed with water, The purity of sodium chromate crystals obtained after drying is 99.5%. After washing and drying the iron slag, it was determined that the total chromium content was 0.4%.
Embodiment 2
[0025] NaOH-NaNO recycled back to the reactor 3 Medium, after NaOH was added, the temperature was raised to 350°C, chromite ore was added, air was introduced, and the reaction was carried out under complete mixing conditions for 4 hours, wherein the weight ratio of NaOH to ore was 2:1, and NaNO 3 The weight ratio with ore is 0.6:1. Finally get NaOH-NaNO 3 The mixed reaction product of medium, chromium salt and iron slag, the conversion rate of chromium is 99.5%. The mixed reaction product is leached with the iron slag washing solution, the lye is separated from the leaching slurry first, and then the iron slag is separated from the sodium chromate leaching solution; the sodium chromate solution is evaporated and crystallized, and the crystal is rinsed with water, The purity of sodium chromate crystals obtained after drying was 99.0%. After the iron slag was washed and dried, it was determined that its total chromium content was 0.15%.
Embodiment 3
[0027] NaOH-NaNO recycled back to the reactor 3 Medium, after NaOH is added, the temperature is raised to 400°C, chromite is added, a mixed gas of air and oxygen with an oxygen volume content of 50% is introduced, and the reaction is carried out for 1 hour under complete mixing conditions, wherein the weight ratio of NaOH to ore is 1.5:1, NaNO 3 The weight ratio with ore is 0.2:1. Finally get NaOH-NaNO 3 The mixed reaction product of medium, chromium salt and iron slag, the conversion rate of chromium is 99.5%. The mixed reaction product is leached with the iron slag washing solution, the lye is separated from the leaching slurry first, and then the iron slag is separated from the sodium chromate leaching solution; the sodium chromate solution is evaporated and crystallized, and the crystal is rinsed with water, The purity of sodium chromate crystals obtained after drying was 98.8%. After the iron slag was washed and dried, it was determined that its total chromium content...
PUM
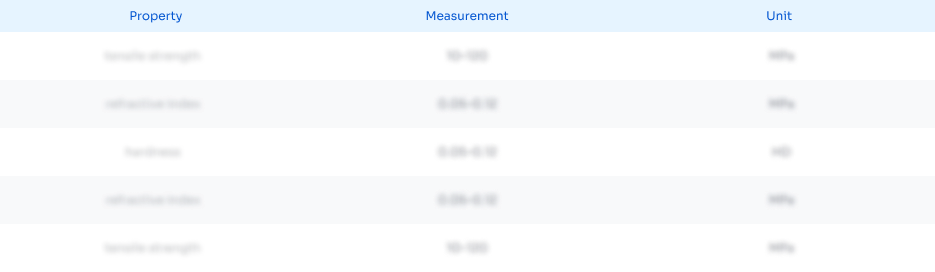
Abstract
Description
Claims
Application Information

- Generate Ideas
- Intellectual Property
- Life Sciences
- Materials
- Tech Scout
- Unparalleled Data Quality
- Higher Quality Content
- 60% Fewer Hallucinations
Browse by: Latest US Patents, China's latest patents, Technical Efficacy Thesaurus, Application Domain, Technology Topic, Popular Technical Reports.
© 2025 PatSnap. All rights reserved.Legal|Privacy policy|Modern Slavery Act Transparency Statement|Sitemap|About US| Contact US: help@patsnap.com