Wet-pressing molding centralized drainage vacuum system
A centralized, wet-pressing technology, used in ceramic molding machines, inductor/transformer/magnet manufacturing, circuits, etc., can solve problems such as unfavorable modern production, large maintenance workload, and low vacuuming efficiency, achieving simple structure, lightening The effect of maintenance volume and convenient operation
- Summary
- Abstract
- Description
- Claims
- Application Information
AI Technical Summary
Problems solved by technology
Method used
Image
Examples
Embodiment Construction
[0016] Depend on figure 1 As shown, 1 and 2 in the figure are two groups of reciprocating vacuum pumps in the centralized drainage vacuum system of the present invention, wherein 2 groups of reciprocating vacuum pumps are under normal production conditions (while the other group is standby during equipment maintenance, to ensure Continuous normal production), in which each group can be equipped with 1 to 5 vacuum pumps; 4 in the figure is a negative pressure vacuum tank with a volume of 2 to 10m 3 ; A three-way valve 3 is provided at the junction of each reciprocating vacuum pump and the negative pressure vacuum tank 4 to adjust the vacuum degree of the system; at the same time, the vacuum tank is connected with 1 to 3 water vapor separators 6, and the water vapor The top outlet port of the separator 6 is connected to the mold of each hydraulic press 8 through the hot-melt PC plastic pipe anticorrosion pipeline, the valve 7 and the hot-melt PC plastic pipe underground pipeline...
PUM
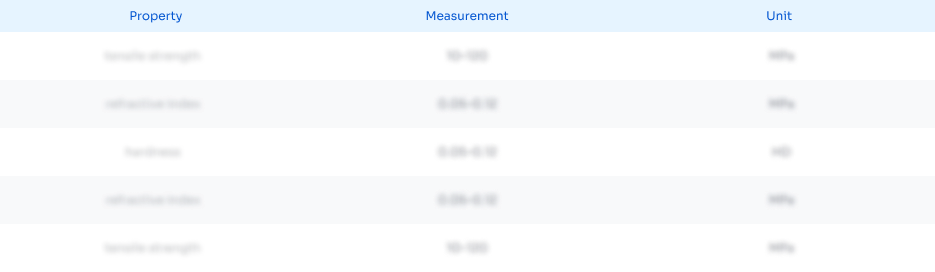
Abstract
Description
Claims
Application Information

- R&D
- Intellectual Property
- Life Sciences
- Materials
- Tech Scout
- Unparalleled Data Quality
- Higher Quality Content
- 60% Fewer Hallucinations
Browse by: Latest US Patents, China's latest patents, Technical Efficacy Thesaurus, Application Domain, Technology Topic, Popular Technical Reports.
© 2025 PatSnap. All rights reserved.Legal|Privacy policy|Modern Slavery Act Transparency Statement|Sitemap|About US| Contact US: help@patsnap.com