Method for preventing lining plate of ball grinder from cracking
A ball mill liner and ball mill technology, applied in the direction of furnace types, furnaces, heat treatment furnaces, etc., can solve the problems of equipment management and production organization, affect the operation rate and efficiency of the ball mill, and break the grid liner of the ball mill, etc., to improve the operating time The effect of processing capacity, reducing downtime, and improving utilization factor
- Summary
- Abstract
- Description
- Claims
- Application Information
AI Technical Summary
Problems solved by technology
Method used
Examples
Embodiment Construction
[0016] Because the high manganese steel lining board has poor thermal conductivity and large thermal expansion coefficient, it is easy to generate thermal stress and structural stress. Therefore, for the lining board with simple shape, thin and uniform thickness, and no accumulation in the furnace, it can be directly quenched by medium and high speed; and For liners with complex shapes, large and heavy pieces, great disparity in thickness, and stacked furnaces, preheating and uniform temperature should be carried out at 650-680 °C above the temperature AC1 at which austenite begins to form when the lining plate is heated. Studies have shown that the longer the holding time above AC1, the more brittle phases are dissolved, which can not only reduce the occurrence of casting cracks, but also reduce the brittle phases, reduce the temperature difference between the inside and outside, and reduce the thermal stress and structural stress, thereby reducing the Casting crack tends to i...
PUM
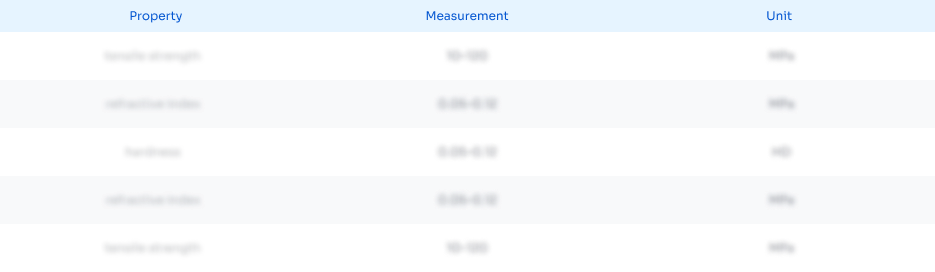
Abstract
Description
Claims
Application Information

- R&D
- Intellectual Property
- Life Sciences
- Materials
- Tech Scout
- Unparalleled Data Quality
- Higher Quality Content
- 60% Fewer Hallucinations
Browse by: Latest US Patents, China's latest patents, Technical Efficacy Thesaurus, Application Domain, Technology Topic, Popular Technical Reports.
© 2025 PatSnap. All rights reserved.Legal|Privacy policy|Modern Slavery Act Transparency Statement|Sitemap|About US| Contact US: help@patsnap.com