Timing control system and method for non-salient pole permanent magnet synchronous motor
A technology for permanent magnet synchronous motors and control systems, which can be used in control systems, single motor speed/torque control, vector control systems, etc., and can solve problems such as increasing the hardware cost of drive control systems
- Summary
- Abstract
- Description
- Claims
- Application Information
AI Technical Summary
Problems solved by technology
Method used
Image
Examples
Embodiment 1
[0085] Embodiment 1, a speed regulation control system of a hidden pole type permanent magnet synchronous motor, such as figure 1 As shown, it includes: proportional integral differential unit PID, Park inverse transform Inverse Park unit, space voltage vector pulse width modulation algorithm SVPWM unit, voltage source inverter VSI, comparator, and measurement unit.
[0086] The measuring unit is used to measure the electrical angle position θ of the rotor of the hidden pole permanent magnet synchronous motor and the mechanical speed ω of the motor m .
[0087] In this embodiment, the measuring unit may include:
[0088] Position measurer, multiplier and differentiator.
[0089] The position measuring device is used to measure the mechanical angular position θ of the rotor m , respectively sent to the multiplier and differentiator; in this embodiment, the position measuring device can be, but not limited to, a code disc installed on the motor shaft end of the hidden pole pe...
Embodiment 2
[0107] Embodiment 2, a speed regulation control method of a hidden pole permanent magnet synchronous motor, comprising:
[0108] Measure the electrical angle position θ of the rotor of the hidden pole permanent magnet synchronous motor and the mechanical speed ω of the motor m ;
[0109] Get the preset target speed ω m * and ω m the difference;
[0110] Perform proportional, integral, and differential operations on the difference to obtain the q-axis voltage component command value u q * ;
[0111] According to θ for u d * and the u q * Perform PARK inverse transformation to obtain the voltage vector u on the stationary coordinate system α * and u β * ; Among them, the u d * is 0;
[0112] According to the voltage vector u α * and u β * , using the space voltage vector pulse width modulation algorithm to generate the pulse width signal of the power device;
[0113] Generate three-phase winding current i according to the pulse width signal of the power dev...
PUM
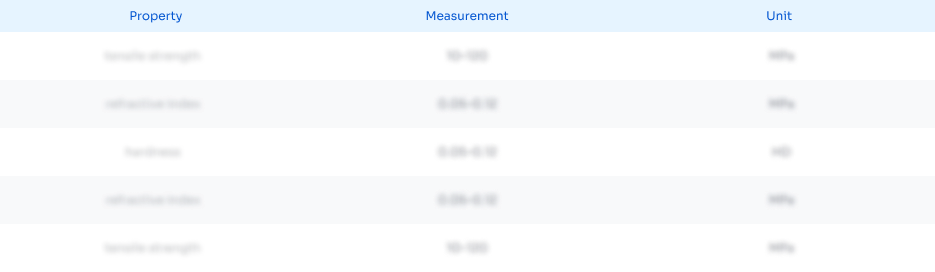
Abstract
Description
Claims
Application Information

- Generate Ideas
- Intellectual Property
- Life Sciences
- Materials
- Tech Scout
- Unparalleled Data Quality
- Higher Quality Content
- 60% Fewer Hallucinations
Browse by: Latest US Patents, China's latest patents, Technical Efficacy Thesaurus, Application Domain, Technology Topic, Popular Technical Reports.
© 2025 PatSnap. All rights reserved.Legal|Privacy policy|Modern Slavery Act Transparency Statement|Sitemap|About US| Contact US: help@patsnap.com