Directly-pushing connecting pipe joint
A technology for connecting pipes and elastic openings, applied in the direction of pipe/pipe joint/pipe fitting, sleeve/socket connection, passing components, etc., can solve problems such as difficulties, rising material costs and processing costs, waste materials, etc., and achieve convenient processing and formation , Saving raw materials and reducing costs
- Summary
- Abstract
- Description
- Claims
- Application Information
AI Technical Summary
Problems solved by technology
Method used
Image
Examples
Embodiment Construction
[0035] Such as figure 1 Shown is the closest structural cross-sectional view of the prior art. There is a gap 13 between the groove of the sealing rubber ring in the through hole of the joint body and the innermost end of the horn hole. To be thicker, or to increase the pipe processing costs for a second time.
[0036] In addition, see figure 2 , Which is figure 1 When the pipe joint is inserted by the connecting pipe, the snap ring is deadlocked. Because the big end of the horn hole is always closed at the end, it must be over-connected with the through hole that adapts to the outer diameter of the connected pipe. This is bound to have an excessive arc. When the radius of the excessive arc is larger than the pitch diameter of the circular elastic snap ring, it will happen that the elastic snap ring will die on the excessive circle of the large end of the horn hole when the connected pipe is inserted. In the arc position and cannot be expanded, the connected tube cannot be inse...
PUM
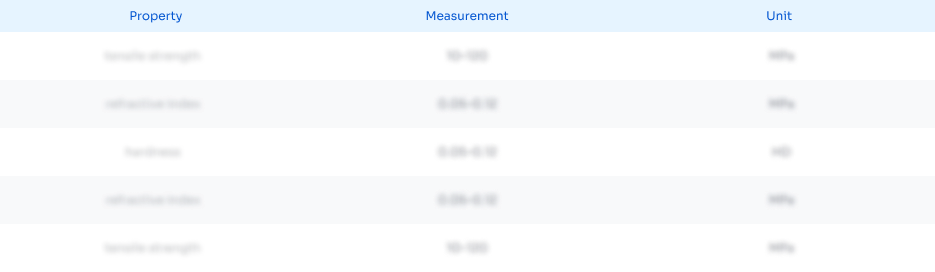
Abstract
Description
Claims
Application Information

- R&D
- Intellectual Property
- Life Sciences
- Materials
- Tech Scout
- Unparalleled Data Quality
- Higher Quality Content
- 60% Fewer Hallucinations
Browse by: Latest US Patents, China's latest patents, Technical Efficacy Thesaurus, Application Domain, Technology Topic, Popular Technical Reports.
© 2025 PatSnap. All rights reserved.Legal|Privacy policy|Modern Slavery Act Transparency Statement|Sitemap|About US| Contact US: help@patsnap.com