Wind power generation unit blade reinforced with needle fiber and fabrication process thereof
A fiber-reinforced, wind turbine technology, applied in the field of blades, can solve the problems of increased blade weight, high raw material cost, and increased blade cost, and achieve the effects of increasing resin inflow speed, increasing layer shear strength, and good impact resistance
- Summary
- Abstract
- Description
- Claims
- Application Information
AI Technical Summary
Problems solved by technology
Method used
Image
Examples
Embodiment 1
[0016] Embodiment 1: as figure 1 As shown, a needle-punched fiber-reinforced wind turbine blade includes a laminated fiber cloth layer 1, a matrix resin material 2 and fibers 3, and the fibers 3 are vertically densely distributed on the laminated fiber cloth layer 1, and the laminated fiber cloth layer A matrix resin material 2 is impregnated between the plies 1 . The matrix resin material 2 is selected from epoxy resin or polyester resin. The fiber cloth layer 1 is a glass fiber cloth layer.
[0017] The manufacturing process of the needle-punched fiber-reinforced wind turbine blade includes the following steps in sequence: (1) Mold preparation: cleaning the mold, removing impurities on the surface of the mold; (2) Fiber cloth laying: laying the glass fiber cloth according to the design It is required to be laid in the cleaned mold to form a laminated glass fiber cloth layer 1; (3) fiber needle punching: use a barbed needle 4 (such as figure 2 As shown) the glass fiber is...
PUM
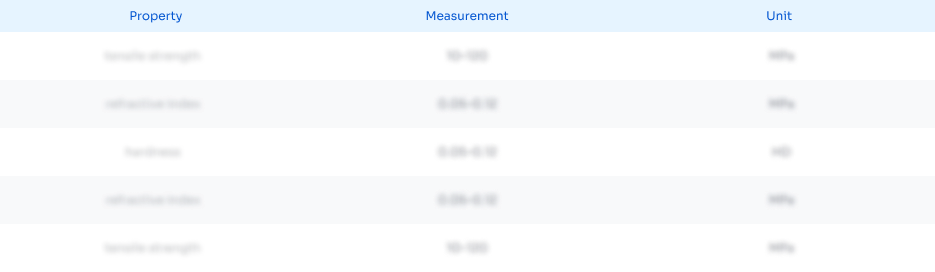
Abstract
Description
Claims
Application Information

- R&D
- Intellectual Property
- Life Sciences
- Materials
- Tech Scout
- Unparalleled Data Quality
- Higher Quality Content
- 60% Fewer Hallucinations
Browse by: Latest US Patents, China's latest patents, Technical Efficacy Thesaurus, Application Domain, Technology Topic, Popular Technical Reports.
© 2025 PatSnap. All rights reserved.Legal|Privacy policy|Modern Slavery Act Transparency Statement|Sitemap|About US| Contact US: help@patsnap.com