Synthetic method and special equipment for nitrobenzene
A synthesis method and technology of nitrobenzene, applied in the preparation of nitro compounds, organic chemistry, etc., can solve the problems of low conversion rate of benzene nitration, achieve the effects of short start-up and shutdown time, increase selectivity, and avoid process fluctuations
- Summary
- Abstract
- Description
- Claims
- Application Information
AI Technical Summary
Problems solved by technology
Method used
Image
Examples
Embodiment 1
[0043] take attached figure 1 As shown in the nitrification process, the mixed acid is pumped to the micro mixer to prepare the nitrification mixed acid, and a mixed acid of sulfuric acid and nitric acid containing 68.5wt% sulfuric acid, 13.2wt% nitric acid and 18.3wt% water is prepared, and the mixed acid flows into the micromixer together with benzene reactor. The channel volume of the microreactor is 154 microliters, the mass ratio of nitric acid to benzene is 1.04, and the liquid hourly space velocity based on the total amount of benzene and mixed acid is 2400h -1 . Due to the exothermic process of the nitration reaction, the product temperature at the outlet of the microreactor is 39.8°C; a section of the nitration product stream enters the stirred reactor and is stirred for 30 minutes under normal pressure and at a speed of 200 rpm. Operate at room temperature. The organic phase in the product is washed with water, alkali and water until neutral to obtain a nitrobenze...
Embodiment 2
[0046] Process and technology are with embodiment 1. Only the molar ratio of nitric acid to benzene, the key reaction material, was changed to 1.16. The pump was run for 10 minutes and stirred for 30 minutes. Because the amount of nitric acid is slightly higher than that of Example 1, the highly dispersed primary nitration product has a temperature of 51° C. at the outlet of the microreactor.
[0047] The obtained total conversion of benzene was 99.92 mol%, and the selectivity of nitrobenzene was 99.85 mol%.
PUM
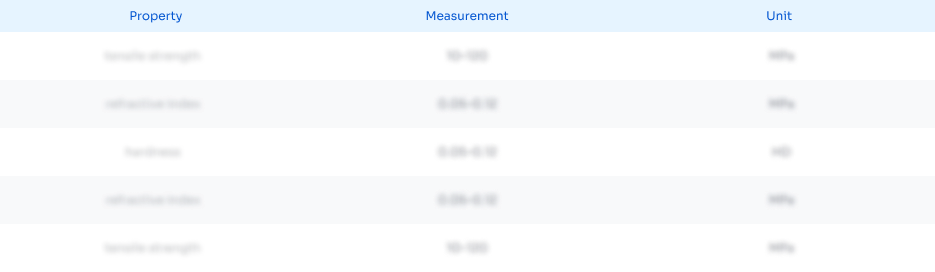
Abstract
Description
Claims
Application Information

- R&D
- Intellectual Property
- Life Sciences
- Materials
- Tech Scout
- Unparalleled Data Quality
- Higher Quality Content
- 60% Fewer Hallucinations
Browse by: Latest US Patents, China's latest patents, Technical Efficacy Thesaurus, Application Domain, Technology Topic, Popular Technical Reports.
© 2025 PatSnap. All rights reserved.Legal|Privacy policy|Modern Slavery Act Transparency Statement|Sitemap|About US| Contact US: help@patsnap.com