Thermosetting paint composition, thermosetting paint film forming method and painting object
A thermosetting, composition-based technology, applied in the direction of surface coating liquid devices, epoxy resin coatings, coatings, etc., can solve problems such as high failure rate, blistering or pinholes
- Summary
- Abstract
- Description
- Claims
- Application Information
AI Technical Summary
Problems solved by technology
Method used
Image
Examples
Embodiment approach
[0052] The thermosetting coating composition of the present invention is a thermosetting coating composition that forms a coating film by coating on the surface of a porous material having a plurality of fine pores on the coating surface and thermally curing it, including: forming a coating film by heating and curing The thermosetting resin component, the solvent component that dissolves the thermosetting resin component, and the self-regenerating component of the coating film. The self-regenerating component of the coating film is formed by heating in the first heating temperature range up to 110°C after the coating is applied. After bubbles in the pores of the material cause cracks in the coating film, the coating film remelts the components that block the bubbles in the second heating temperature range above 110°C and before the thermosetting temperature.
[0053] Here, the difference between the present invention and the prior art will be described using the drawings.
[0...
Embodiment 1
[0109] Example 1 is an example in which the addition of acetylmalic acid was 5% by weight. In the first heating temperature step (first heating step), the temperature was raised from 90 to 125°C over 30 minutes (temperature increase rate: 1.17°C / min). In addition, in the second heating temperature step (second heating step), the temperature was raised from 125°C to 160°C over 30 minutes (temperature increase rate: 1.17°C / min). In addition, in the third heating temperature step (third heating step), the resin was cured by heating at 160° C. for 20 minutes.
Embodiment 2
[0111] Example 2 is an example in which the addition of acetylmalic acid was 5% by weight. In the 1st heating temperature process (1st heating process), after holding at 90 degreeC for 10 minutes, it heated up to 125 degreeC over 5 minutes. Moreover, in the 2nd heating temperature process (2nd heating process), after holding at 125 degreeC for 10 minutes, it heated up to 160 degreeC over 5 minutes. And in the 3rd heating temperature process (3rd heating process), it heated at 160 degreeC for 20 minutes, and hardened resin.
PUM
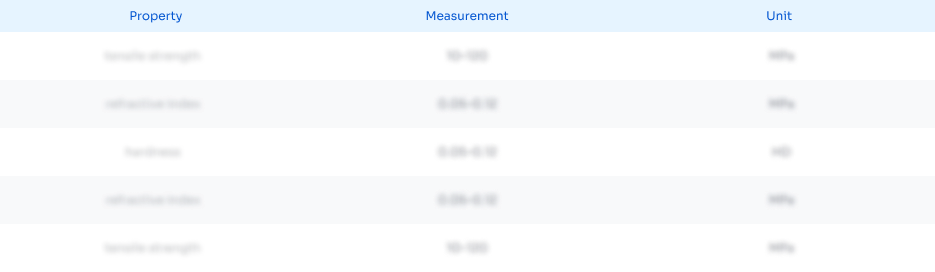
Abstract
Description
Claims
Application Information

- R&D
- Intellectual Property
- Life Sciences
- Materials
- Tech Scout
- Unparalleled Data Quality
- Higher Quality Content
- 60% Fewer Hallucinations
Browse by: Latest US Patents, China's latest patents, Technical Efficacy Thesaurus, Application Domain, Technology Topic, Popular Technical Reports.
© 2025 PatSnap. All rights reserved.Legal|Privacy policy|Modern Slavery Act Transparency Statement|Sitemap|About US| Contact US: help@patsnap.com