Process for producing seamless steel pipe made of high-chromium high-nickel alloy steel
A technology for seamless steel pipes and manufacturing methods, applied in metal rolling, manufacturing tools, metal rolling, etc., can solve the problems of longer rolling time, no inspiration, shortened plug life, etc., to prevent internal surface marks, improve The effect of service life
- Summary
- Abstract
- Description
- Claims
- Application Information
AI Technical Summary
Problems solved by technology
Method used
Image
Examples
Embodiment 1
[0074] In order to confirm the effect of the present invention, a steel billet with a diameter of 225 mmφ and a length of 2 to 4 m was made of a high Cr-Ni base alloy containing C: 0.019%, Cr: 26.0%, Ni : 32.3%, Mo: 3.2%, and P: 0.028%, and the rest is composed of Fe and impurities. The billet is heated to 1180-1260°C, and then the punching ratio is 1.5-3.0, and the roll concave is 2.28-5.31m / s. Peripheral speed of the groove was carried out in cross-rolling piercing experiments. Table 1 shows the results of evaluation of melting marks on the inner surfaces of steel pipes produced by various manufacturing methods.
[0075] Table 1
[0076] Table 1
[0077]
No.
billet plus
heat temperature
(℃)
Perforation ratio
Formula 1)
Calculated
whether
Suit
-ln(t h / r o )
Roller peripheral speed
V f
(m / sec)
melting crack
Evaluation
1
2
3
4 ...
Embodiment 2
[0082] In addition, a steel slab with a diameter of 225 mmφ and a length of 5 to 10 m made of a high Cr-Ni base alloy containing C: 0.019%, Cr: 26.0%, Ni: 32.3%, Mo : 3.2% and P: 0.028%, and the remainder is composed of Fe and impurities. The billet was heated to 1210°C, and then cross-rolled piercing experiments were carried out at a piercing ratio of 1.7 to 2.3 and a peripheral speed of the roller groove of 3.5m / s. . The number of cycles until the front end of the plug was melted and lost in the rolling of billets of various pipe lengths and could not be used in the next rolling was investigated. As shown below, when the length of the tube blank is greater than 7m, the service life of the plug is extremely shortened.
[0083] Tube blank length Cycle times
[0084] 5m 4 times
[0085] 6m 4 times
[0086] 7m 3 times
[0087] 8m 1 time
[0088] 9m 0 times
[0089] 10m 0 times
PUM
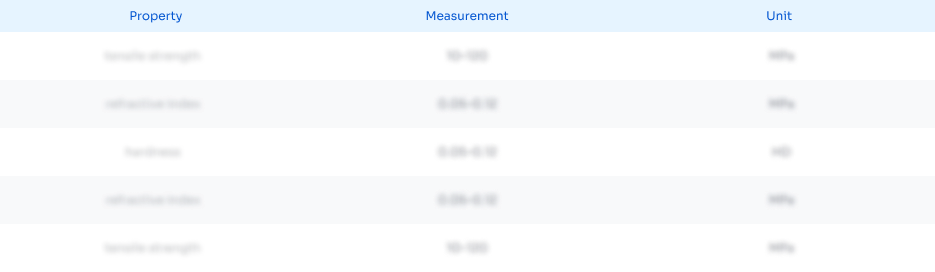
Abstract
Description
Claims
Application Information

- R&D Engineer
- R&D Manager
- IP Professional
- Industry Leading Data Capabilities
- Powerful AI technology
- Patent DNA Extraction
Browse by: Latest US Patents, China's latest patents, Technical Efficacy Thesaurus, Application Domain, Technology Topic, Popular Technical Reports.
© 2024 PatSnap. All rights reserved.Legal|Privacy policy|Modern Slavery Act Transparency Statement|Sitemap|About US| Contact US: help@patsnap.com