Multifunctional laser holography stamping process
A laser holography and molding technology, applied in printing, printing presses, decorative arts, etc., can solve the problems of adverse effects of laser pattern printing process, inconsistent molding products, and high plate wheel, avoiding the phenomenon of smearing, improving the quality of printing pressure, The best laser effect
- Summary
- Abstract
- Description
- Claims
- Application Information
AI Technical Summary
Problems solved by technology
Method used
Image
Examples
Embodiment Construction
[0012] Below in conjunction with embodiment and accompanying drawing, the present invention will be further described:
[0013] This embodiment is a laser holographic embossing machine for embossing patterns on RVC films. The embossing group has a structure of two embossing stations. The position of the slit on the plate wheel is monitored by the photoelectric eye. The adjustment of the PLC control circuit of the motor makes the plate seams staggered during the molding of the two stations to improve the quality of the printing. The structure of this embodiment is as shown in the drawings, including frame 1, beam 2, tensioning wheel 3, guide wheel a 4, preheating wheel 5, first molding station, tension control group, second molding station, Guide wheel bb16, ironing wheel 17, rubber pressure wheel 18, cooling wheel 19, printing film 20, photoelectric eye and PLC control circuit, the installation sequence is: the left and right frame 1 is supported by 5 middle beams 2, and the p...
PUM
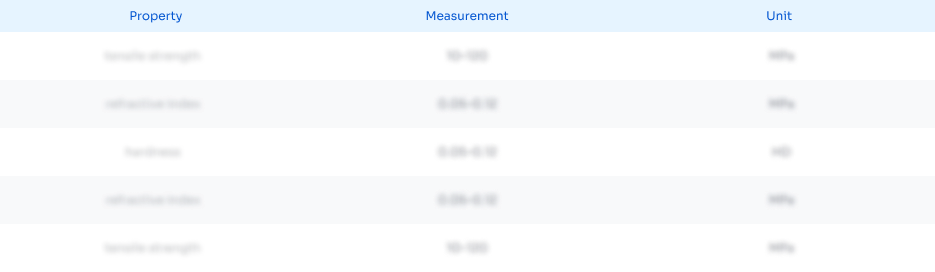
Abstract
Description
Claims
Application Information

- Generate Ideas
- Intellectual Property
- Life Sciences
- Materials
- Tech Scout
- Unparalleled Data Quality
- Higher Quality Content
- 60% Fewer Hallucinations
Browse by: Latest US Patents, China's latest patents, Technical Efficacy Thesaurus, Application Domain, Technology Topic, Popular Technical Reports.
© 2025 PatSnap. All rights reserved.Legal|Privacy policy|Modern Slavery Act Transparency Statement|Sitemap|About US| Contact US: help@patsnap.com