Production process of embossed lens local transfer product
A production process and lens technology, applied in decorative arts, decorative structures, etc., can solve the problems of poor embossed lens effect, misalignment, and opacity, and achieve the effects of high cost performance, low production cost, and easy operation.
- Summary
- Abstract
- Description
- Claims
- Application Information
AI Technical Summary
Problems solved by technology
Method used
Examples
Embodiment 1
[0030] A kind of production technology of partial transfer product of relief lens, it comprises the following steps:
[0031] Step 1, engraving mesh rolls: the first layer of mesh rolls and the second layer of mesh rolls are engraved according to customer needs;
[0032] Step 2, double sizing coating: use the first layer of mesh roll and the second layer of mesh roll to carry out two sizing coatings, and reach 2.5g / m 2 The dry amount of gluing is obtained to obtain the first layer of transfer coating; wherein, the glue used for gluing coating contains ammonia water with a mass fraction of 2%, which can prevent the glue from spreading, and the edges of the pattern and text appear rough after the transfer; and the coating of the glue The amount is 5.5g / m 2 ;
[0033] Step 3, film coating: the first layer of transfer coating obtained in step 2 is transferred to the film through the mesh roll of the coating machine, and the coating is dried by the coating machine oven to obtain ...
Embodiment 2
[0041] A kind of production technology of partial transfer product of relief lens, it comprises the following steps:
[0042] Step 1, engraving mesh rolls: the first layer of mesh rolls and the second layer of mesh rolls are engraved according to customer needs;
[0043] Step 2, double sizing coating: use the first layer of mesh roll and the second layer of mesh roll to carry out two sizing coatings, and reach 2g / m 2 The dry weight of gluing is obtained to obtain the first layer of transfer coating; wherein, the glue used for gluing coating contains ammonia water with a mass fraction of 1%, which can prevent the glue from spreading, and the edges of the pattern and text appear rough after the transfer; and the coating of the glue The amount is 5g / m 2 ;
[0044] Step 3, film coating: the first layer of transfer coating obtained in step 2 is transferred to the film through the mesh roll of the coating machine, and the coating is dried by the coating machine oven to obtain the ...
Embodiment 3
[0052] A kind of production technology of partial transfer product of relief lens, it comprises the following steps:
[0053] Step 1, engraving mesh rolls: the first layer of mesh rolls and the second layer of mesh rolls are engraved according to customer needs;
[0054] Step 2, double sizing coating: use the first layer of mesh roll and the second layer of mesh roll to carry out two sizing coatings, and reach 3g / m 2 The dry weight of gluing is obtained to obtain the first layer of transfer coating; wherein, the glue used for gluing coating contains ammonia water with a mass fraction of 4%, which can prevent the glue from spreading, and the edges of the pattern and text appear rough after the transfer; and the coating of the glue The amount is 6g / m 2 ;
[0055] Step 3, film coating: the first layer of transfer coating obtained in step 2 is transferred to the film through the mesh roll of the coating machine, and the coating is dried by the coating machine oven to obtain the ...
PUM
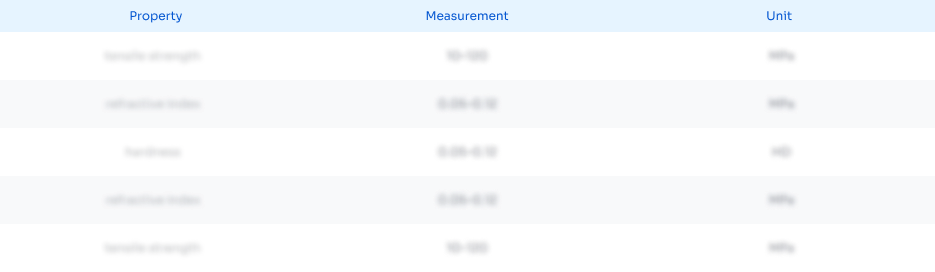
Abstract
Description
Claims
Application Information

- Generate Ideas
- Intellectual Property
- Life Sciences
- Materials
- Tech Scout
- Unparalleled Data Quality
- Higher Quality Content
- 60% Fewer Hallucinations
Browse by: Latest US Patents, China's latest patents, Technical Efficacy Thesaurus, Application Domain, Technology Topic, Popular Technical Reports.
© 2025 PatSnap. All rights reserved.Legal|Privacy policy|Modern Slavery Act Transparency Statement|Sitemap|About US| Contact US: help@patsnap.com