A kind of laser master film for film pressure transfer film and its preparation method and application method
A transfer film, laser film technology, applied in the direction of transferring ink from the original, applying liquid to the surface, coating, etc., can solve the problem of limiting the service life of the laser film, shortening the service life of the laser plate, and damage to the laser nickel plate. and other problems, to achieve the effect of improving the bottom folding resistance of the coating, reducing energy consumption and saving production costs.
- Summary
- Abstract
- Description
- Claims
- Application Information
AI Technical Summary
Problems solved by technology
Method used
Image
Examples
Embodiment 1
[0030] A kind of laser mother film that is used for film pressure transfer film of this embodiment, such as figure 1 As shown, it includes PET film 1, coating coating 2, laser film lamination 3 and aluminum plating layer 4 laminated in sequence.
[0031] The preparation method of this laser mother film comprises the following steps:
[0032] Step 1, prepare coating paint: take by weighing 30% acrylic resin, 2% cellulose acetate, 38% n-propyl acetate, 5% cellulose acetate and 25% leveling agent respectively, the acrylic resin, cellulose acetate Mix plain element, n-propyl acetate, cellulose acetate and leveling agent and stir evenly to obtain coating coating, stand-by;
[0033] Step 2, coating coating: using PET film 1, coating the coating coating prepared above on PET film 1, drying the coating coating to obtain coating coating 2;
[0034] Step 3, laser film pressure: laser film pressure is carried out on the above-mentioned coating layer 2 to obtain a laser film laminate la...
Embodiment 2
[0039] A kind of laser mother film that is used for film pressure transfer film of this embodiment, such as figure 1 As shown, it includes PET film 1, coating coating 2, laser film lamination 3 and aluminum plating layer 4 laminated in sequence.
[0040] The preparation method of this laser mother film comprises the following steps:
[0041] Step 1, prepare coating paint: take by weighing 50% acrylic resin, 4% cellulose acetate, 30% n-propyl acetate, 1% cellulose acetate and 15% leveling agent respectively, the acrylic resin, cellulose acetate Mix plain element, n-propyl acetate, cellulose acetate and leveling agent and stir evenly to obtain coating coating, stand-by;
[0042] Step 2, coating coating: using PET film 1, coating the coating coating prepared above on PET film 1, drying the coating coating to obtain coating coating 2;
[0043] Step 3, laser film pressure: laser film pressure is carried out on the above-mentioned coating layer 2 to obtain a laser film laminate la...
Embodiment 3
[0048] A kind of laser mother film that is used for film pressure transfer film of this embodiment, such as figure 1 As shown, it includes PET film 1, coating coating 2, laser film lamination 3 and aluminum plating layer 4 laminated in sequence.
[0049] The preparation method of this laser mother film comprises the following steps:
[0050] Step 1, prepare coating paint: take by weighing 40% acrylic resin, 3% cellulose acetate, 25% n-propyl acetate, 2% cellulose acetate and 30% leveling agent respectively, the acrylic resin, cellulose acetate Mix plain element, n-propyl acetate, cellulose acetate and leveling agent and stir evenly to obtain coating coating, stand-by;
[0051] Step 2, coating coating: using PET film 1, coating the coating coating prepared above on PET film 1, drying the coating coating to obtain coating coating 2;
[0052] Step 3, laser film pressure: laser film pressure is carried out on the above-mentioned coating layer 2 to obtain a laser film laminate la...
PUM
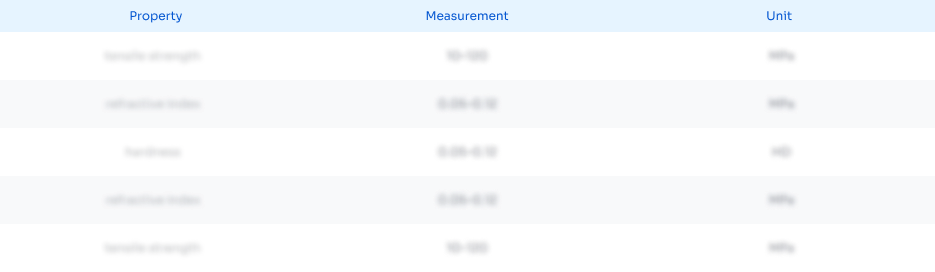
Abstract
Description
Claims
Application Information

- Generate Ideas
- Intellectual Property
- Life Sciences
- Materials
- Tech Scout
- Unparalleled Data Quality
- Higher Quality Content
- 60% Fewer Hallucinations
Browse by: Latest US Patents, China's latest patents, Technical Efficacy Thesaurus, Application Domain, Technology Topic, Popular Technical Reports.
© 2025 PatSnap. All rights reserved.Legal|Privacy policy|Modern Slavery Act Transparency Statement|Sitemap|About US| Contact US: help@patsnap.com